We do have Staghorn Sumac here in southern Ontario, and I have turned some, still have pieces sitting in my storage, it seems to grow slower than what you have there Michael, there are other species, one is called Poison Sumac { also called Swamp Sumac) with the same/similar poisonous outcome as Poison Ivy and poison Oak, rash and blisters, though I do not know what it looks like, or if it grew in the London area, over here in NW Ontario no Sumac growsA friend gave me a couple of chunks of Sumac a long while ago (not sure what species). One of those situations where the wood looked so crummy you almost want to say no. BUT, I had never turned Sumac, so I couldn’t pass it up. It sat, and sat, and sat, until today when I decided to turn a mini-calabash out of it. The wood was super dry, super soft, hollow-pith, but very beautiful. Green and brown colors and wide growth rings. Here are before, during, and after shots:
View attachment 61135
View attachment 61136
View attachment 61137

I just now went to the storage and shop, had to close them, as I had them opened up to warm up some, like it is around 5-6 degrees C, and like the shop was below freezing (cooling water by the grinder was solid ice) we had a couple of cold nights -29C, much warmer now ;-))
Anyway took a couple pictures of a Sumac log I have sitting and the turned bowl from the largest end of the Staghorn wood I had, kind of a bird-beak shape, and I don't like it, so it sits.
I also have smaller pieces sitting in the shop, might use them someday, though that Pith in it is a nuisance.
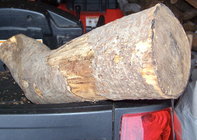
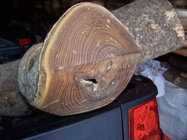
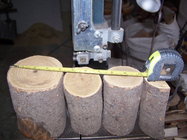
Last edited: