Time to cut the body! This step has been looming over me for a while, as it's the last stressful part of the project (stressful in the sense that a total disaster could occur). First I needed to lay out my cuts in a way that left my lid exactly at the top--somewhat of a challenge with a round-body object. Dividers to the rescue! Because I took the time to make sure I had perfectly equal halves and also centered my glue line on the exterior, I had a starting point. I needed to mark 90 degrees from my glue line, so I used my dividers to get close, and then made two pencil marks the same distance from the glue line. Then, I marked a line in the middle of my pencil marks, and used a square to draw a line that connected both sides of the teapot. ind of a weird thing to explain, so hopefully the following image clarifies my strategy. The photo shows dividers on the glue line and my first mark. the next step was to put one side of the dividers on the glue line opposite the lid and mark with a pencil where the other point landed.
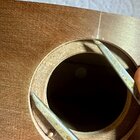
Following this, I measured 110mm down from the top--this is past the center point, so will allow the body of my teapot to curve under a bit. I then used my dividers and my middle pencil line to draw boundaries for my cut line. I opened my dividers so that one point touched the pencil line, and the other point touch a spot on the edge 110mm down from center. I marked this point with a pencil, and then repeated this three more times (with the dividers set at the same measurement). Then it was just a matter of connect the dots with a straight edge. All of these steps gave me a cut line that wrapped around the body, and once cut would establish the lid perfectly on top.
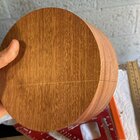
Time to cut. I don't have a band saw, this is way too big for my scroll saw, and I couldn't be bother to clean off my table saw (that's a half joke--I wasn't too keen on trying to cut this cleanly with my cheap table saw). I decided the best course of action would be to use my flush cut saw. It has a narrow kerf and fine teeth. Also, the nose is slightly angled and lacks teeth, so as long as you move slowly you can get a clean, straight, and square cut. Here is a shot with the nose recessed into the cut line--you should be able to imagine how this helps saw on track.
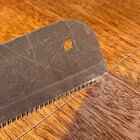
After some sawing, I finally made it through, with just a little bit of cleanup required. Here is the glory shot of the teapot sections separate:
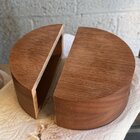
The smaller section is waste (or something for a future project, of course), and the larger piece is the teapot body.
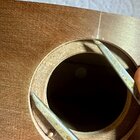
Following this, I measured 110mm down from the top--this is past the center point, so will allow the body of my teapot to curve under a bit. I then used my dividers and my middle pencil line to draw boundaries for my cut line. I opened my dividers so that one point touched the pencil line, and the other point touch a spot on the edge 110mm down from center. I marked this point with a pencil, and then repeated this three more times (with the dividers set at the same measurement). Then it was just a matter of connect the dots with a straight edge. All of these steps gave me a cut line that wrapped around the body, and once cut would establish the lid perfectly on top.
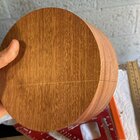
Time to cut. I don't have a band saw, this is way too big for my scroll saw, and I couldn't be bother to clean off my table saw (that's a half joke--I wasn't too keen on trying to cut this cleanly with my cheap table saw). I decided the best course of action would be to use my flush cut saw. It has a narrow kerf and fine teeth. Also, the nose is slightly angled and lacks teeth, so as long as you move slowly you can get a clean, straight, and square cut. Here is a shot with the nose recessed into the cut line--you should be able to imagine how this helps saw on track.
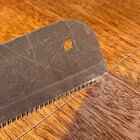
After some sawing, I finally made it through, with just a little bit of cleanup required. Here is the glory shot of the teapot sections separate:
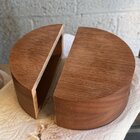
The smaller section is waste (or something for a future project, of course), and the larger piece is the teapot body.
Last edited: