Router fluting jigs need a large base so they don't tip in usage. The one linked to in post #46 has too small a base. It has holes in the base that I assume are to screw it to large base.
In Paul Howard’s original instructions for his jig (he no longer sells them himself) there was mention of fitting it to a larger base if required.
My home made jig is pretty much the same size as the PH jig and I’ve never experienced any tendency for it to tip as you suggest.
A guy called William Hunt has produced a series of videos of the PH jig in use and I don’t recall him using a larger base?
Before making my jig I did look on the net for inspiration from other users and once again I don’t remember seeing any jigs with what I might term a large base. I’d be interested in seeing one though if you have a kink Doug as I may be missing something?
I should add that Paul Howard mentions using a PVC plate on the bottom of his jig. It is though the same size as the alloy base.
I decided to mount my base on PTFE buttons to make it easy to slide and this works extremely well. I also use other jig components not used on the PH jig such as guide rails and pivot points. I didn’t consider it at the time I drew up my plans but a large base would certainly preclude or at the least make it difficult for me to use some of these other components.
I also made a “pivot base” but have not used it yet apart from a quick test. The mounting is hanging upside down in the picture in case anyone wondered. The part is obviously used in place of the normal long base.
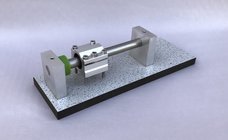