I’ve had several people ask me to post my process on how I make my heart bowls.
I had thought about submitting this to AAW for a magazine article several months ago but just don’t have time at this point to do that.
Quick Background: Three years ago I was turning in my shop and knowing my wife loves hearts I started thinking about turning her a heart bowl. I didn’t want to turn a bowl and then bandsaw the heart out of it so I had to come up with a way to get a uniform shape and I wanted the minimum steps possible to achieve this. Having a fairly extensive background in drafting and design I came up with this sitting at my table saw with a compass, graph paper and scissors
.
1. Determine the size heart you want to make, with me this was determined by the size of the wood I had to work with. I get free drops of 8/4-10/4 walnut, cherry, oak, and maple from a local company.
2. Once you determine the size draw a circle on paper, I use graph paper, the size of the heart. The CENTER POINT of the circle is very important as you will see later.
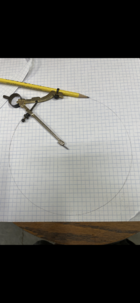
3. Draw half a heart in one side of the circle and fold the paper on the centerline of the circle and cut the shape out.
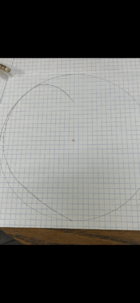
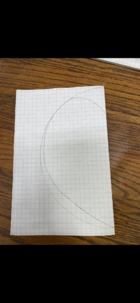

I had thought about submitting this to AAW for a magazine article several months ago but just don’t have time at this point to do that.
Quick Background: Three years ago I was turning in my shop and knowing my wife loves hearts I started thinking about turning her a heart bowl. I didn’t want to turn a bowl and then bandsaw the heart out of it so I had to come up with a way to get a uniform shape and I wanted the minimum steps possible to achieve this. Having a fairly extensive background in drafting and design I came up with this sitting at my table saw with a compass, graph paper and scissors

1. Determine the size heart you want to make, with me this was determined by the size of the wood I had to work with. I get free drops of 8/4-10/4 walnut, cherry, oak, and maple from a local company.
2. Once you determine the size draw a circle on paper, I use graph paper, the size of the heart. The CENTER POINT of the circle is very important as you will see later.
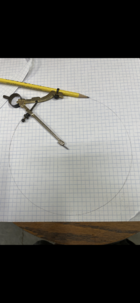
3. Draw half a heart in one side of the circle and fold the paper on the centerline of the circle and cut the shape out.
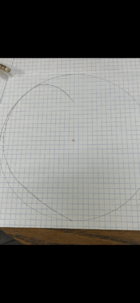
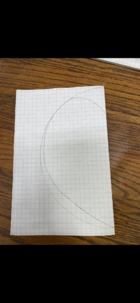
