I have searched the forum to try to find an answer but nothing specific enough for my question.
I am looking for options to use as a filler for intentional gaps on a piece I am working on (inspired from a piece I saw from Mayuko Wood Craft).
First off, I do not have a pressure/vacuum pot and do not plan on getting one.
I want to fill gaps as you can see in the photo. The gaps are roughly 3/8" deep and no more than an 1/8" wide. They surround the entire vessel. I will also need to tint/color it black.
At first, I had my heart set on resin. However, reality set in and I realized I do not want to go through the hassle and time to create dams, pour in sections and all that. *Unless someone has an easy suggestion for it.
In my mind, what little is left of it, I think a paste or very thick liquid would be best since the piece is round. The inspirational piece was filled with wood glue mixed with coconut shell charcoal power.
Finally, I would like to finish it with a wipe-on poly gloss.
Thoughts?
Thank you
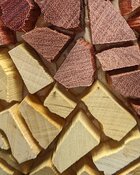
I am looking for options to use as a filler for intentional gaps on a piece I am working on (inspired from a piece I saw from Mayuko Wood Craft).
First off, I do not have a pressure/vacuum pot and do not plan on getting one.
I want to fill gaps as you can see in the photo. The gaps are roughly 3/8" deep and no more than an 1/8" wide. They surround the entire vessel. I will also need to tint/color it black.
At first, I had my heart set on resin. However, reality set in and I realized I do not want to go through the hassle and time to create dams, pour in sections and all that. *Unless someone has an easy suggestion for it.
In my mind, what little is left of it, I think a paste or very thick liquid would be best since the piece is round. The inspirational piece was filled with wood glue mixed with coconut shell charcoal power.
Finally, I would like to finish it with a wipe-on poly gloss.
Thoughts?
Thank you
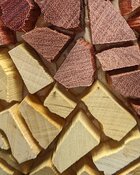