Our town was settled by Norwegian fishermen, and we still celebrate Norwegian independence day (mostly for tourism). Part of the parade is vendors downtown, which are locals ranging from small children selling candy to retired people selling knitting. Last year my dad and I sold our turnings on two stacked totes. We sold to tourists for cheap prices on the sidewalk. The largest purchase was a large yellow cedar bowl for $85 US. A couple of weeks ago, we flew to a larger town in Alaska so my dad could get a medical appointment. In the larger town, with much more tourism, and people, a gallery sold a yellow cedar bowl for the same price, but the bowl was less than half the diameter. Yellow cedar has virtually no variation between trees, the wood was identical, and the designs of both were pretty bad, but at the end of the day, I was selling on the sidewalk, and the other turner was selling in a gallery. His bowl took less than 10% of the wood my bowl blank was.As I don't have to pay it directly out of my own pocket I don't think of it as a cost, but gallery commission would also be the largest $ component of getting a piece of wood through to a sale in the gallery. The galleries take close to half of the retail price, however, I don't begrudge them any of that. They earn every bit of their cut and selling directly to customers is the last thing I would want to be doing myself. Without the galleries I couldn't continue to turn, which is what I like to be doing.
I do spend some of my surplus income from my turning buying bowl gouges that I don't really need, but find interesting, however, that is not a necessary cost to keep me turning; it's just a peripheral indulgence to keep me amused...![]()
I think I need to make work that appeals to a higher-paying clientele before I try to sell to them. Maybe eventually.
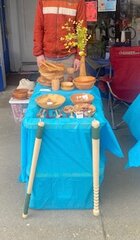