Was able to finish this Cottonwood burl bowl this evening. Tore up some of my sanding discs and paper, but did manage reasonably well. This is the bowl I was working on when I mentioned about using a Sharpie pen to ID spots while turning. As you can see, the problem void was reduced a little, but the wall thickness was a major problem, and couldn't go any further than this.....did turn out good enough to sell, though.....someone out there wants a really gnarly Cottonwood burl bowl! Big voids have always been a real problem for my style of multi-faceted turning.....but, I don't let that prevent me from acquiring great examples when I see them!
The photo on the left shows some great chatoyance showing up in the interior.....this nice attribute will be enhanced when it gets the Beall 3-step buff treatment.
-o-
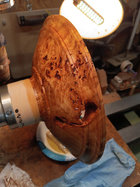
The photo on the left shows some great chatoyance showing up in the interior.....this nice attribute will be enhanced when it gets the Beall 3-step buff treatment.

-o-
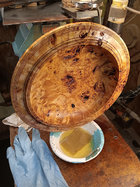
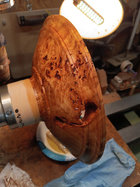
Last edited: