Will do. I ordered a 30mm Silver Tip knot earlier along with some Arko. Mitchell's is my favorite but have been wanting to try some Arko.Michael, you're welcome. And Monty, they're dirt simple to turn, really. Brad has suggested drilling width and depth for the inset for different sized brush knots right there on the ordering page. I like 24mm the best, and get the SHD (super-high density) knots for my fancier brushes. I set the knots with 5-minute epoxy, though silicone glue works too. You don't want to set the knot too deep, or the brush will be too stiff. If you do drill too deep with your forstner bit, you can raise the knot back up with a coin or two under it. I just set the knot on this last one with a couple of nickels epoxied under it to get the right loft. Please show us your work if you go down this rabbit hole!
Finished turned and started the sanding and finishing routine. ~9x4 pecan calabash. Sanded with 80 grit and applied Seal Coat sanding sealer. This one soaked up so much sanding sealer that I'm going to give it a day or two to dry. This one has some really nice grain.
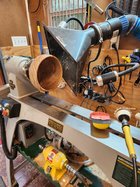