I turned some eucalyptus this afternoon. Completely green, cut from a log I picked up a few weeks ago.
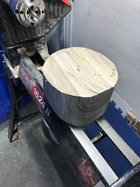
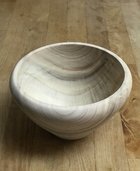
I really struggled with a couple of things:
1) Even though it was green wood, it was really difficult to create the exterior shape. The wood just seemed really hard. This was the second blank from this log and the first one was easy to shape. Could the blank have dried enough in a week to make that much of a difference?
2) I had terrible tool marks on the inside. Some are still slightly visible. Seemed like I kept falling off the bevel so I'd have to go back and try to pick it up. Each time I left a minute trace of the original cut.
Definitely not an enjoyable experience. Though the aroma was very pleasant. So there's that.
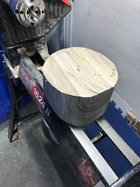
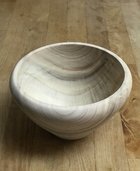
I really struggled with a couple of things:
1) Even though it was green wood, it was really difficult to create the exterior shape. The wood just seemed really hard. This was the second blank from this log and the first one was easy to shape. Could the blank have dried enough in a week to make that much of a difference?
2) I had terrible tool marks on the inside. Some are still slightly visible. Seemed like I kept falling off the bevel so I'd have to go back and try to pick it up. Each time I left a minute trace of the original cut.
Definitely not an enjoyable experience. Though the aroma was very pleasant. So there's that.