Quick tip.
I keep many tools without handles in a shallow drawer behind me when I'm at the lathe, and in other places.
I make custom inserts for tool handles, mount the bare tools in the handles when needed, then often hang them on a wall.
But when in the drawer, the sharpened tools are vulnerable to damage. This is especially true for the extremely sharp cutters on the Hunter tools.
In addition to damage in the shop, the tools can really get damaged when transporting to and from a demo or class.
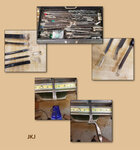
To protect the ends I make cheap but effective protectors from plastic tubing. I once went to the hardware store
and bought 3' of every size of clear plastic tubing they had - so handy for many things!
To make the tool tip protectors I cut off a short piece of tubing that will fit snugly on a tool. Heat the end with a
small heat gun until the plastic softens, then squeeze the end together with some pliers.
Sometimes I don't even bother with closing up the ends but just use the piece of tubing.
These work well!
JKJ
I keep many tools without handles in a shallow drawer behind me when I'm at the lathe, and in other places.
I make custom inserts for tool handles, mount the bare tools in the handles when needed, then often hang them on a wall.
But when in the drawer, the sharpened tools are vulnerable to damage. This is especially true for the extremely sharp cutters on the Hunter tools.
In addition to damage in the shop, the tools can really get damaged when transporting to and from a demo or class.
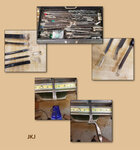
To protect the ends I make cheap but effective protectors from plastic tubing. I once went to the hardware store
and bought 3' of every size of clear plastic tubing they had - so handy for many things!
To make the tool tip protectors I cut off a short piece of tubing that will fit snugly on a tool. Heat the end with a
small heat gun until the plastic softens, then squeeze the end together with some pliers.
Sometimes I don't even bother with closing up the ends but just use the piece of tubing.
These work well!
JKJ