My 2 cents on the recess thing. I’m enjoying this thread immensely!
That, no customers have complained about recesses, is hardly a ringing endorsemen.
There is no, or not to my knowledge, historical precedent for recesses on bowls. Ceramics, glass, hand carved, or baskets.
They effect the design of one’s piece. Allowance has to make regarding the thickness at the center of your bowl, so you loose that ‘spoon feel’, going from one rim to the other side smoothly, without changes and bumps or flat spots. Tough to do without making it paper thin at the recess.
It serves no purpose, other than being a left-over, a tell, from your methodology. Like a belly button. Had a purpose for a short time, now a left-over. In the case of the b.b. there are no options.
In our case, however, there is. So I respectfully suggest that you are giving, and leaving the attachment, unnecessarily.
A foot fixes the issue, as does a smooth round bottom. So, why not do one of those?
I strive to make each of my pieces, mine alone, as much as possible. So, I start with green logs and work from there. I consider everything, every cut, every curve, thickness here and there, from complex to simple decisions. A zillion decisions and ponderings, which make our art so fabulous. I’m just not willing to do all that, to call it my own if I’ve bailed at this critical part of our expression. I’m a great bowl turner, but I don’t do feet?
Do judges even comment about recesses? Like, ‘what a clever recess. Can you share the story of how you came to that?’
I doubt it, because it’s a non part of the piece.
Marc
Apologies for the delayed response, but I’ve been mulling over your thoughtful posting...
Apologies also for the longer ramble following, some of it at a tangent and off topic to the OP, but I do get back to tenon/recess widths towards the end…
On customer endorsement...
Whatever we think about the aesthetic judgement of our customers, if they stop buying our pieces we will eventually have to stop making them. Not that their preferences should be the only determinant of what we make, but in the end they are the final arbiters. I always begin with a focus on each individual piece of wood I'm working with with little regard for where it might go after I'm aesthetically and craft-wise satisfied with the outcome. My practice is then to leave those pieces on display in various places about my house so that I can get a fresh look at them, at least until I can't accommodate any more. From those I then select the next batch to go to the gallery. Some of that decision is about what best goes with what...
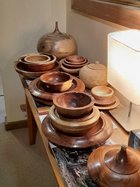
The next arbiter might be the gallery owner/director deciding if my work meets their standard or style or market segment. I went through that selection process a very long time ago and nowadays they just accept whatever I take to them. Almost everything I take eventually sells and at a rate that is about comfortable for me to keep providing new work. Price is a factor in that, but not always. All of my higher priced pieces have sold, but occasionally there are some pieces that don't move in a reasonable time and they get removed from the display to keep it fresh. Some of those get recycled later back on display and sell and there are just a very few pieces (like the one in my avatar) that eventually get pulled from the gallery altogether and these become gifts for family and friends. In fairness to my fellow exhibitors I never discount my pieces and the gallery never bargains on price with customers.
So, for me, no matter what my aesthetic judgement may be about my work, it is the gallery clients who are the final arbiters of my pieces. By and large, they will not be as critical of my work as myself in terms of aesthetics and craft. Few, if any of them, will know or care about the nuances of form and finish, or for that matter feet, that we woodturners may anguish over. But, without their endorsement, which they do by purchasing our work, we don’t get to make more of what we think has merit.
~~~
On competition judges as arbiters of what is good in terms of aesthetics and craft...
I must admit I have no experience as either a judge or having my work formally judged since graduating art college over half a century ago. My grades back then were some indication that my aesthetic judgement was sound. I did also teach for a while in art and design at tertiary level, so was in effect making judgement on student work back then, but that was a long time ago. It may be different elsewhere, but Richard Raffan has said to me a number of times that the standard of woodturning here in Australia is quite low and, besides Richard himself, I would be hard put to find someone here whose judgement I would value. That is not to say that I don’t admire the work of others from around the world, which we can now see at least online nowadays. And, I like to keep learning from my own efforts and from others on forums like this one.
Local clubs and the like are another source of critique for their members. That is a good starting point if you have access to one of those at least in your early turning years. Their limitation is of course the limitation of its collective membership. For example, if you happened to be a member of the ACT Woodcraft Guild in Canberra, where Richard Raffan is a member, you would be very fortunate. But, the guidance in many other local clubs can be quite limited. Then there are clubs and associations that bring in the best turners from around the world for demo weekends and the like, and they can lift the level of turning among the participants, albeit with a bit of cloning that can follow.
For one reason and another, I haven’t had much exposure to such clubs and organisations, but I do have a circle of artist/artisan friends and colleagues and they readily express their opinions, free of charge, which is a form of judgement for what it is worth!
~~~
On there being... "no historical precedent for recesses on bowls. Ceramics, glass, hand carved, or baskets."
That misses the point I was trying to make, so my mistake, I probably wasn't clear enough in what I wrote. What I was attempting to say is that how an item was made isn't so obsessively disguised in other media as it seems to be in the case with woodturning. Leaving a recess in the foot of a woodturned piece is just an example of allowing the making process to remain in the finished piece. Here are three examples of allowing the making process to remain on the feet of some ceramic pieces in my collection...
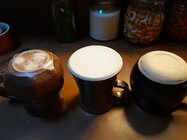
None of that evidence of the making process on the foot of those pieces would be considered among the potters I know as a failure to complete the pieces. On the contrary, they are evidence of competent execution. Potters invariably turn over a piece to look for that evidence. I also always do the same with woodturned pieces that deserve closer attention. I’m looking to be delighted by what I find there. Far too often all I find there is a shallow featureless concave depression with the type of information inscribed there that is more suited to an entry in a catalogue that is more typical of an inscription on a souvenir. And, not the sort of thing you would expect to find on a piece of ceramics, cabinetry or glass in a national or state gallery collection. A maker's mark, yes, but not souvenir style information. No surprise that the fine art institutions don’t take woodturning seriously… :~}
~~~
Back to the recess itself…
For clarity, I do make a tenon when turning the outside of a green blank and use that to hold the piece when I’m green turning the inside, but then use a recess for the final seasoned turning of the inside of the piece.
For reference, here is the bottom of a piece with what I call a recess (mortice/mortise, if you prefer that term) that was on the lathe yesterday before reversing to return the inside. That is what I am referring to.
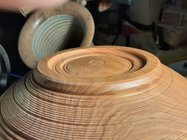
Several have commented to the effect that having/leaving a recess eliminates the option of having ‘a foot’. I presume what is meant there is that using and retaining a recess would restrict or prevent some feet options. I’m not sure where the notion comes from that using and retaining a recess would do that. Design wise I use whatever foot suits the piece and that is not limited in any way by using and retaining a recess during the final turning stage.
Likewise, I can’t think of any shape, inside or out, that is restricted by using a recess for the final turning. As the majority of the design decisions are made at the blank cutting and green turning stages, leaving the bottom of a bowl too thin by adding a recess is minimised. And, it seems to me that there is so little difference between what is left in the bottom of a piece between using a recess and dishing it when a tenon is turned off… it isn't a consideration.
Here is the remaining bottom of an experimental test piece that was laying around in the workshop that I have sawn in half to show the foot profile and recess. The top of that piece had previously been turned away during testing that I was doing for something, so the foot is no longer in proportion to the remaining walls, which are thinner than I would normally turn making the foot ring disproportionately larger than I would make it, but it servers the purpose of showing the recess that I use in making ‘the foot’ on bowls and other forms ...
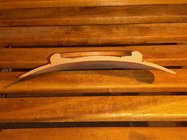
Not much difference there between the depth of the recess and what would remain if dishing the bottom after removing the tenon.
My foot designs do require a deft hand when doing the final tuning out of the inside of pieces to avoid them splitting apart and/or letting go. As you would expect, they don't take too kindly to a catch, but fortunately they happen very rarely nowadays.
Getting back to OP’s original question, the width of the shoulder in the ‘recess’ has two functions; to ensure the piece is held securely in the chuck, but it is also a design element in the finished item. Getting the balance right between those two functions exercises both craft and aesthetic judgement.
For my part, I really can’t think of many of the pieces that I make that would be compromised in their design by my using a recess as the holding method for completing the insides of the piece. I don’t consider the recesses that I leave as unfinished business. I give them as much attention as any other design aspect of the piece as that is where my maker's mark goes, and as far as I know, nobody has referred to my recesses as ‘belly buttons’, but if they did, that’s OK too…
There are many satisfactory ways of going about things and I contend that using the recess on pieces the way I do is an effective and efficient technique with acceptable aesthetic outcomes. Perhaps not suited to every turner, but still a very satisfactory option for some of us.
That’s at least my 5c worth, so I will stop my rambling and leave it at that Marc, et al.