.
One of the drawbacks for gouges made from tungsten carbide (TC) is that it is best sharpened with diamond. Many of us now have CBN grinding wheels for sharpening our HSS turning tools and although those could be used to sharpen TC that would be both inefficient (something like only 67% efficient as diamond) and would also shorten the life of the CBN wheel for use with HSS, which is its primary purpose.
With their wider use, the cost of CBN wheels have progressively come down in recent years at the same time as diamond wheels have gone up with their lesser use. With the exception of the diamond wheels made specifically to fit on Tormek style machines, quality diamond wheels that will run on a bench grinder are now costing upward of twice to three times more than a similar sized CBN wheel. So, few of us are going to go to the expense of having a diamond wheel in our workshops, in addition to our CBN wheels, for just sharpening TC.
Of course, if you happen to already have a:
However, few of us do have those options, so that leaves the challenge of finding an economical way of sharpening TC tools with diamond.
Most of us do have a few handheld diamond plates that we use to freshen an edge on our turning tools and they will also do a good job of doing that on TC, albeit slowly and without the benefit of being able to use jigs and attachments to maintain angles, etc. The thin single sided diamond discs that are used in lapidary for shaping and polishing gems are made in the same way as the handheld diamond plates we have been using and compared to diamond wheels are relatively inexpensive. In lapidary they are mounted horizontally on a platen and grind with water. I experimented with mounting the discs vertically on the side of my 8” CBN wheel and set up my gouge jig to sharpen against the discs in two ways…
With the first method I attached a cleat with a jig leg pivot point to the back of my sharpening platform…
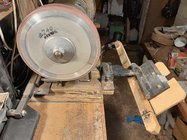
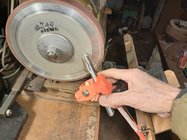
Any of the swing away sharpening platforms could have this method added to them. If you don’t already have a sharpening platform on your grinder you could rig up something similar for just this purpose. Ensuring that its axis at the pivot point is square to the grinder axis is the key requirement.
This method has the advantage of allowing a TC tip if mounted on a longer shaft to swing unimpeded to get the full grind back along both wings. This method will produce a different grind pattern on the bevel to what you will get with wheel grinding, but as far as I could tell that didn’t affect the performance of the gouge edge.
The other method I tried was to use a slide with a pivot point mounted on the bench top square to the end of the grinder with the grinder raised (I needed to do that by 2”) to accommodate the length of the jig leg that I normally use. Here is that setup…
Both the left and right sides of the disc need to be used to fully grind back both wings.
This setup works well with shorter gouge bars like the one shown in the above photo, but if a longer shaft is attached to the carbide tip the overall length of that is restricted with that setup. The maximum length of shaft + TC tip was 10” with my setup doing a 42° bevel grinding using a Tru-Grind jig. This overall length could be extended by raising the grinder further off the bench and also raising the height of the slide so that the grind contact point is maintained at grinder axis height. I found that grinding at axis height was necessary with a 6” disc to allow my jig to swing past the outer diameter of the 8” wheel when grinding the wings.
Another way to setup so that the length of the gouge shaft will not be an issue is to position the bench grinder so that the side of the wheel hangs out over the edge of the bench, but I couldn’t find a way of positioning the slide that I used so that the pivot point for the leg of the jig was away from the side of the bench without the clamp on the slide being located somewhere underneath the grinder. I have an idea of how to get around that, but haven't implemented it as I don’t have a need for longer shafts at this stage.
One of the drawbacks for gouges made from tungsten carbide (TC) is that it is best sharpened with diamond. Many of us now have CBN grinding wheels for sharpening our HSS turning tools and although those could be used to sharpen TC that would be both inefficient (something like only 67% efficient as diamond) and would also shorten the life of the CBN wheel for use with HSS, which is its primary purpose.
With their wider use, the cost of CBN wheels have progressively come down in recent years at the same time as diamond wheels have gone up with their lesser use. With the exception of the diamond wheels made specifically to fit on Tormek style machines, quality diamond wheels that will run on a bench grinder are now costing upward of twice to three times more than a similar sized CBN wheel. So, few of us are going to go to the expense of having a diamond wheel in our workshops, in addition to our CBN wheels, for just sharpening TC.
Of course, if you happen to already have a:
- Tormek with a diamond wheel on it then you are good to go… :~}
- Diamond wheel for your bench grinder, as some still do, ditto!
- Sorby ProEdge sharpener or similar, just swap in a diamond belt on that…
- Using one of those diamond belts on a DIY belt grinder is another option.
However, few of us do have those options, so that leaves the challenge of finding an economical way of sharpening TC tools with diamond.
Most of us do have a few handheld diamond plates that we use to freshen an edge on our turning tools and they will also do a good job of doing that on TC, albeit slowly and without the benefit of being able to use jigs and attachments to maintain angles, etc. The thin single sided diamond discs that are used in lapidary for shaping and polishing gems are made in the same way as the handheld diamond plates we have been using and compared to diamond wheels are relatively inexpensive. In lapidary they are mounted horizontally on a platen and grind with water. I experimented with mounting the discs vertically on the side of my 8” CBN wheel and set up my gouge jig to sharpen against the discs in two ways…
With the first method I attached a cleat with a jig leg pivot point to the back of my sharpening platform…
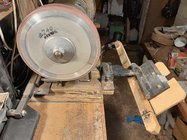
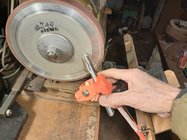
The sideways position of the cleat determines the correct sharpening angle against the disc. Once the cleat is fixed in position, that sharpening angle will be maintained regardless of how the platform is swung in and out, which will be done to get a position where the gouge tip won’t intersect with the wheel retaining nut or flange while being sharpened. The platform can be swung down out of the way or back into position for platform sharpening after using it this way and the correct setting will be maintained for when it is needed for sharpening TC next time.Any of the swing away sharpening platforms could have this method added to them. If you don’t already have a sharpening platform on your grinder you could rig up something similar for just this purpose. Ensuring that its axis at the pivot point is square to the grinder axis is the key requirement.
This method has the advantage of allowing a TC tip if mounted on a longer shaft to swing unimpeded to get the full grind back along both wings. This method will produce a different grind pattern on the bevel to what you will get with wheel grinding, but as far as I could tell that didn’t affect the performance of the gouge edge.
The other method I tried was to use a slide with a pivot point mounted on the bench top square to the end of the grinder with the grinder raised (I needed to do that by 2”) to accommodate the length of the jig leg that I normally use. Here is that setup…
Both the left and right sides of the disc need to be used to fully grind back both wings.
This setup works well with shorter gouge bars like the one shown in the above photo, but if a longer shaft is attached to the carbide tip the overall length of that is restricted with that setup. The maximum length of shaft + TC tip was 10” with my setup doing a 42° bevel grinding using a Tru-Grind jig. This overall length could be extended by raising the grinder further off the bench and also raising the height of the slide so that the grind contact point is maintained at grinder axis height. I found that grinding at axis height was necessary with a 6” disc to allow my jig to swing past the outer diameter of the 8” wheel when grinding the wings.
Another way to setup so that the length of the gouge shaft will not be an issue is to position the bench grinder so that the side of the wheel hangs out over the edge of the bench, but I couldn’t find a way of positioning the slide that I used so that the pivot point for the leg of the jig was away from the side of the bench without the clamp on the slide being located somewhere underneath the grinder. I have an idea of how to get around that, but haven't implemented it as I don’t have a need for longer shafts at this stage.