I really do enjoy my 9-month-old Oneway 1224. Size, power, luxury car ride... Except, I am just not enamored with the U-joint yoke style locking handle for the tool rest on the banjo, not from day 1. If I recall, it is the same style of handle on all of their lathes, but possibly a smaller handle and thread size. The handle is riveted into a yoke which threads into the banjo. Yes, the banjo collar the yoke threads into can be re-oriented clockwise/counterclockwise to suit the user and change the angle the handle hangs at, but I just do not like that loose-in-the-yoke style handle. But I can't help but wonder, why didn't they just spec an "adjustable handle"? These are the type of handle where the handle is attached to a threaded stud, and by way of a spring and gear teeth, the handle can be reset to any different position on the threaded stud. So, I went looking, and found what I hope will be the solution I'm seeking.
2 pics, factory yoke-style handle.
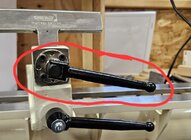
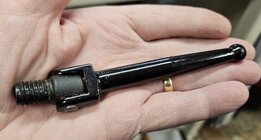
A German company called Kipp makes these adjustable handles (and I get the feeling that maybe they developed this style of handle a long time ago). They are available for a low price ($ teens) with a fiber re-enforced plastic handle, or a mid-price ($ 20's) cast zinc handle, both available on Amazon, Grainger, MSC, etc., or the high price ($30's) with a steel handle that I can only find from the USA rep in Michigan. Establishing that the thread is a 1/2" x 13 thread pitch (after torturing myself to conclude that it could be a very uncommon M12 x 2 thread pitch metric), I found 2 steel handle Kipp versions. I bought this first one below, because other than the silver color, the general shape of it is similar to the shape of the banjo cam lock lever. I could always paint it if I want to. The handle length is a little bit shorter than stock (1/2" or so, no functional loss there), and the threaded stud length is 20mm rather than the 15mm of the Oneway handle, so if needed I'll trim down the stud length, about 3-4mm. The adjustable handle is offset from the threaded stud at 20 degrees, which I mocked up on the lathe with the factory handle, and 20 degrees is about perfect.
www.kippusa.com
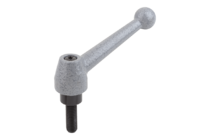
This one below is a bit more streamlined looking, but it came in several colors (plastic, zinc, and steel) like this red (which I was this >< close to buying, just for the splash of color). Maybe if I'm inspired, I'll paint the one above a red color, just for fun. Nearly the same overall dimensions and handle offset as above.
www.kippusa.com
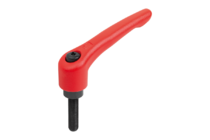
I'm sure the lower cost zinc version would have been sufficient, but if I can get a lifetime piece made from steel instead, I'm going steel. And shipping was, of course, very non-Amazon-like ($16). $51 total. It should be here from Michigan in a few days, and I'll report back on its success (or failure...).
I did some 'net searching, and I could not find another person who felt the same as I do about that yoke-style handle, nor anyone who ever reported a mechanical failure with it. Here I am again, the odd-man out. But, it just bugs me, and it had to go.
2 pics, factory yoke-style handle.
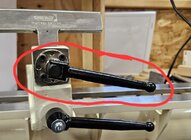
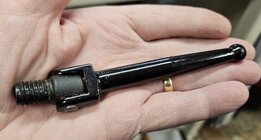
A German company called Kipp makes these adjustable handles (and I get the feeling that maybe they developed this style of handle a long time ago). They are available for a low price ($ teens) with a fiber re-enforced plastic handle, or a mid-price ($ 20's) cast zinc handle, both available on Amazon, Grainger, MSC, etc., or the high price ($30's) with a steel handle that I can only find from the USA rep in Michigan. Establishing that the thread is a 1/2" x 13 thread pitch (after torturing myself to conclude that it could be a very uncommon M12 x 2 thread pitch metric), I found 2 steel handle Kipp versions. I bought this first one below, because other than the silver color, the general shape of it is similar to the shape of the banjo cam lock lever. I could always paint it if I want to. The handle length is a little bit shorter than stock (1/2" or so, no functional loss there), and the threaded stud length is 20mm rather than the 15mm of the Oneway handle, so if needed I'll trim down the stud length, about 3-4mm. The adjustable handle is offset from the threaded stud at 20 degrees, which I mocked up on the lathe with the factory handle, and 20 degrees is about perfect.
Adjustable Handle steel | KIPP USA
Adjustable Handle steel ✓ Made in Germany ✓ Highest quality ✓ Fast delivery ✓ Customer-specific solutions ✓ Download CAD data ✓ Wide range with 75,000 items ✓ Manufacturing expertise ✓ Request a quote ✓ Order online now!

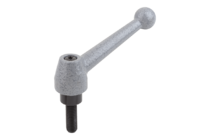
This one below is a bit more streamlined looking, but it came in several colors (plastic, zinc, and steel) like this red (which I was this >< close to buying, just for the splash of color). Maybe if I'm inspired, I'll paint the one above a red color, just for fun. Nearly the same overall dimensions and handle offset as above.
Adjustable Handle steel traffic red RAL 3020 textured matt | KIPP USA
Adjustable Handle steel traffic red RAL 3020 textured matt ✓ Made in Germany ✓ Highest quality ✓ Fast delivery ✓ Customer-specific solutions ✓ Download CAD data ✓ Wide range with 75,000 items ✓ Manufacturing expertise ✓ Request a quote ✓ Order online now!

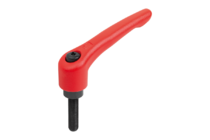
I'm sure the lower cost zinc version would have been sufficient, but if I can get a lifetime piece made from steel instead, I'm going steel. And shipping was, of course, very non-Amazon-like ($16). $51 total. It should be here from Michigan in a few days, and I'll report back on its success (or failure...).
I did some 'net searching, and I could not find another person who felt the same as I do about that yoke-style handle, nor anyone who ever reported a mechanical failure with it. Here I am again, the odd-man out. But, it just bugs me, and it had to go.
Last edited: