As I started in this thread (with 2 videos) https://www.aawforum.org/community/...dest-shop-with-dust-collection-details.23325/ which wandered and meandered with a lot of good information, here is the final result of my version of the Richard Raffan-inspired dust hood I built for my Oneway 1224.
Raffan, nor Tomislav Tomasic in his video, had no plans to build it. It's easy to see that their setups are pretty casual in design, as is mine. Will my plastic bowl collect more effectively than Raffan's angle cut pipe? I don't know, but my bowl hood was my previous dust collector inlet, so I incorporated it. I built my dust box (or hood, or plenum) from dumpster salvaged 1/2" plywood, a $2 plastic kitchen bowl, and a few 4" duct fittings from the hardware store. Net cost, about $20. It's all just screwed together for easy future mods, if needed.
My shelf base is installed 3" below the lathe bed ways, and it comes to about 1/4" of the bed. The height of the dust box walls goes 3" above the top of the lathe swing (12" swing). So, the 4 dust box sides are 18" tall. Two 18"x18" panels, and two 9"x18" panels. That is what my scrap plywood gave me, otherwise I would have made 10" wide small panels rather than 9".
The 45 degree box panel pair (with the white bowl) is the only one attached to the bottom shelf. The 90 degree right panel pair is loose to be set wherever conditions require. My scrap plywood top could have been a few inches longer, but I think what I built will suffice for most of what I'll ever turn on this machine. I hope this inspires potentially better dust collection at your lathe, or at least a few minutes of entertainment.
My dust collector in a 1hp 650cfm Jet 2-bag, with 2 upgraded (20 years ago) 5-micron felt bags which is downstream of a 30-gallon metal trash can with a "cyclone" separator lid to grab big stuff from going to the collector.
With my limited testing of the final product, I am very happy with the result. I'm convinced that containing the dust into the dust box as it comes off the sandpaper is more effective at controlling environmental dust than simply having a collector hose with some version of a hood right behind the spinning wood.
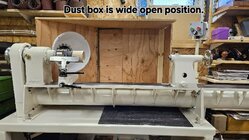
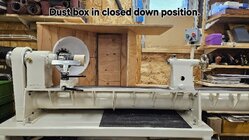
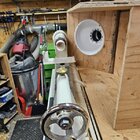
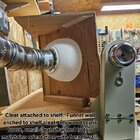
(To be continued...)
Raffan, nor Tomislav Tomasic in his video, had no plans to build it. It's easy to see that their setups are pretty casual in design, as is mine. Will my plastic bowl collect more effectively than Raffan's angle cut pipe? I don't know, but my bowl hood was my previous dust collector inlet, so I incorporated it. I built my dust box (or hood, or plenum) from dumpster salvaged 1/2" plywood, a $2 plastic kitchen bowl, and a few 4" duct fittings from the hardware store. Net cost, about $20. It's all just screwed together for easy future mods, if needed.
My shelf base is installed 3" below the lathe bed ways, and it comes to about 1/4" of the bed. The height of the dust box walls goes 3" above the top of the lathe swing (12" swing). So, the 4 dust box sides are 18" tall. Two 18"x18" panels, and two 9"x18" panels. That is what my scrap plywood gave me, otherwise I would have made 10" wide small panels rather than 9".
The 45 degree box panel pair (with the white bowl) is the only one attached to the bottom shelf. The 90 degree right panel pair is loose to be set wherever conditions require. My scrap plywood top could have been a few inches longer, but I think what I built will suffice for most of what I'll ever turn on this machine. I hope this inspires potentially better dust collection at your lathe, or at least a few minutes of entertainment.
My dust collector in a 1hp 650cfm Jet 2-bag, with 2 upgraded (20 years ago) 5-micron felt bags which is downstream of a 30-gallon metal trash can with a "cyclone" separator lid to grab big stuff from going to the collector.
With my limited testing of the final product, I am very happy with the result. I'm convinced that containing the dust into the dust box as it comes off the sandpaper is more effective at controlling environmental dust than simply having a collector hose with some version of a hood right behind the spinning wood.
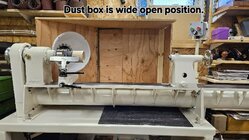
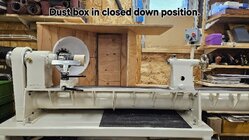
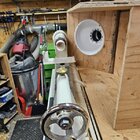
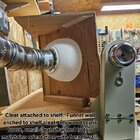
(To be continued...)
Last edited: