Happy Friday, all-Starting my 1st day of Christmas break exploring the PM 3520C I purchased through Woodcraft on their recent 10% off Black Friday sale for $5129, and added the light (which is both powerful, sturdy and infinitely adjustable with all the different planes of travel; it really seems like an integral part of the lathe instead of an accessory). The experience with both Woodcraft and the shipping company were textbook customer service; sometimes you get lucky, though in general I have never regretted a Woodcraft purchase (and I have spent thousands in them). If this reads like a fan-boy post, so be it, but this lathe is just a revelation to me after trading up from my good old Laguna 12/16. And it still sits perfectly level and stable on its leveling feet on the plywood base straddling the main beam of my crowded shop. It took two strapping young tradesmen (my lineman son and a burly neighbor) to help me get it moved in and set up, leveled and wired-up last weekend. At nearly 6 feet, I also added the risers, which on top of the plywood made it a little high for me, but two or three shop mats get me just right and feel better under my feet (after teaching all day on concrete).
For its maiden voyage, I wanted to do something I thought would be relatively predictable, a kiln-dried 10"x3" cherry blank from turningblanks.net (fortunately, they are within driving distance, though they ship nationwide). It turned like a dream, and has a really nice figure after 400-grit, Yorkshire Grit and a couple of coats of TruOil. This thing is so powerful and precise, I feel like I almost immediately became a better turner on it because it is so smooth and stable, which really inspires more confidence on longer cuts and around the bend" on a bowl (which was often treacherous on the Laguna due to my slowly-developing skills and some vibration-induced chatter). I am excited knowing that I haven't even begun to explore all that this lathe is capable of. And the structural heft of it (9/16" silky-smooth cast-iron ways on a 260 lb. cast iron bed), the 160 lbs. headstock along with the precision of the hefty spindle all inspire confidence that was often frustrated by run-out and vibration on the Laguna). The 40 lb. banjo and tool-rest lock like a bank vault when I adjusted them to my liking. And I have to say the chromed locking handles all around are one of the sexiest things I have ever seen on a machine (though it takes some effort to lock the banjo all the way (perhaps a little more adjustment)).
It's just a joy to use, just making every operation more stable and precise. It just makes everything easier, and yet the possibilities seem almost endless.
And if you get one, get the light kit. It's totally worth it. I couldn't find specs, but plenty bright and easily movable and sturdy for inspecting for scratches. Trust me-get the light for about $150 if I recall (though I also got 10% off of it).
I know you're not supposed to get too attached to things, but my family is justified in their concern that I have almost made a shrine of this thing (I have an obsessive personality anyway, which can be both a blessing and a curse).
And yes, I know I need to get rid of that old power-strip, especially since my electrician wired up about 32 total outlets around the shop in addition to the 220 outlet (I've just been so focused on the lathe). Now out to add another coat of TruOil (which I also have a problem with). Happy Holidays/Merry Christmas early, fellow turners! Aaron
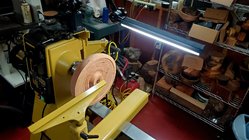
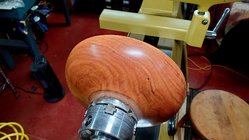
For its maiden voyage, I wanted to do something I thought would be relatively predictable, a kiln-dried 10"x3" cherry blank from turningblanks.net (fortunately, they are within driving distance, though they ship nationwide). It turned like a dream, and has a really nice figure after 400-grit, Yorkshire Grit and a couple of coats of TruOil. This thing is so powerful and precise, I feel like I almost immediately became a better turner on it because it is so smooth and stable, which really inspires more confidence on longer cuts and around the bend" on a bowl (which was often treacherous on the Laguna due to my slowly-developing skills and some vibration-induced chatter). I am excited knowing that I haven't even begun to explore all that this lathe is capable of. And the structural heft of it (9/16" silky-smooth cast-iron ways on a 260 lb. cast iron bed), the 160 lbs. headstock along with the precision of the hefty spindle all inspire confidence that was often frustrated by run-out and vibration on the Laguna). The 40 lb. banjo and tool-rest lock like a bank vault when I adjusted them to my liking. And I have to say the chromed locking handles all around are one of the sexiest things I have ever seen on a machine (though it takes some effort to lock the banjo all the way (perhaps a little more adjustment)).
It's just a joy to use, just making every operation more stable and precise. It just makes everything easier, and yet the possibilities seem almost endless.
And if you get one, get the light kit. It's totally worth it. I couldn't find specs, but plenty bright and easily movable and sturdy for inspecting for scratches. Trust me-get the light for about $150 if I recall (though I also got 10% off of it).
I know you're not supposed to get too attached to things, but my family is justified in their concern that I have almost made a shrine of this thing (I have an obsessive personality anyway, which can be both a blessing and a curse).
And yes, I know I need to get rid of that old power-strip, especially since my electrician wired up about 32 total outlets around the shop in addition to the 220 outlet (I've just been so focused on the lathe). Now out to add another coat of TruOil (which I also have a problem with). Happy Holidays/Merry Christmas early, fellow turners! Aaron
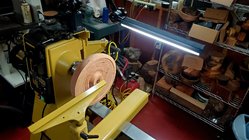
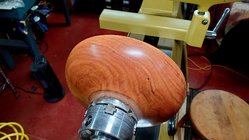