Searching this site under “Norfolk Island Pine,” also abbreviated NIP, yields 14 pages of threads and many beautiful and creative turnings. Whether the wood is true NIP or Cook Island Pine is probably irrelevant. The tree grows in Hawaii, Florida, and California. The unusual aspects of this wood are twofold—the ability to be translucent and the unusual limb pattern that can lend to a “star,” “spokewheel,” or “flower” pattern when carved end grain. The limbs are denser than the trunk wood and dull instruments quickly; they also can fall out and may need stabilization with CA, as may the pith, retained in end grain turnings.
One source for NIP with which I have had success is www.woodturningblanks4u.com, no affiliation, but nice people with a good selection of both end grain and side grain blanks. Here in southern California, one may occasionally find NIP blanks, as I have. To achieve the star pattern requires understanding of the tree anatomy. The limbs all grow from the central pith in a slight upward direction and limbs usually grow at the same level, hence the ability to create the desired star pattern. There can be up to 8 limbs though usually only 5 or 6. When studying the blank, bark removed, one notices that the pith in the limbs is not in the center. If the pith is at the top of the limb, the limb runs downward toward the center of the blank and if in the bottom of the limb, runs upward. Understanding this allows one to orient the blank in such a way as to carve to reveal the desired pattern.
While bowls are usually turned outside first, NIP is turned inside first to reveal the star pattern. Mount the blank on a faceplate, the faceplate on what will be the top or rim of the bowl, then round the blank and create a tenon. Before shaping the outside, reverse the piece onto the tenon and hollow it out to reveal the star pattern. Once this is completed, the outside can be turned. Reverse again to finish the bottom.
Tear out is significant with NIP end grain turnings. Being a neophyte turner, I have not figured out how to avoid or minimize this, though some use scrapers and others use various shaped gouges with better success than I have had—80 grit sandpaper and hours of time are making up for my turning inexperience. Any help in this area would be appreciated.
Ron Kent’s eponymous site www.ronkent.com has many tips regarding NIP and especially stabilization of this wood using an inexpensive 50:50 mix of liquid dishwashing detergent and water. I have found that Smart&Final carries a 5 gallon container of dishwashing detergent at a reasonable price. It is amazing how even a wet piece of NIP will soak up a large amount of this liquid, making subsequent turning quite wet. I have had luck turning the entire piece at one time, then applying several coats of oil, and had no cracks develop, but many advocate twice turning, or placing the once turned piece back in the detergent mixture or some other stabilization concoction. It amazes me how many ounces of tung oil the thirsty turned piece absorbs when oiled. Ron Kent would apply 50 or more coats in a several month process but he obviously had much more patience than I have.
Translucence can be achieved with a combination of a thin turning and how one finishes the piece. I will amend this post after I learn more about this—I have sent emails to a couple of the turners on this site asking how they achieved their NIP translucence—it seems to relate much to the finishing process and soaking of the piece in the appropriate mixture.
Another aspect of NIP is how easily it spalts, offering more unique and interesting patterns to a turning. I’ve read that if additional spalting is desired, some time in a moist environment before turning or in an inflated plastic bag is all that is needed.
While end grain turnings are often done with NIP, some spectacular pieces are created with side grain turnings—just review the 14 pages of NIP on this site to see some amazing work. The woodturning blanks site noted above also has a nice description of how to orient blanks to achieve desired results, including pictures that explain the tree anatomy and blank mounting better than I have written.
I have written this brief piece mainly to help me understand NIP and hopefully to engender some discussion so that I may learn more about this wood and end grain turning. Ron Kent’s turnings are what have inspired me—one of his beautiful bowls was purchased by me almost 40 years ago when in Hawaii—and still remains a favorite among my collection. I hope others will add to this thread and even correct my mistakes and comments.
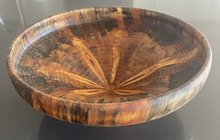
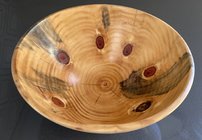
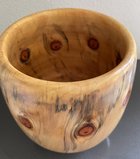
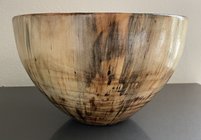
One source for NIP with which I have had success is www.woodturningblanks4u.com, no affiliation, but nice people with a good selection of both end grain and side grain blanks. Here in southern California, one may occasionally find NIP blanks, as I have. To achieve the star pattern requires understanding of the tree anatomy. The limbs all grow from the central pith in a slight upward direction and limbs usually grow at the same level, hence the ability to create the desired star pattern. There can be up to 8 limbs though usually only 5 or 6. When studying the blank, bark removed, one notices that the pith in the limbs is not in the center. If the pith is at the top of the limb, the limb runs downward toward the center of the blank and if in the bottom of the limb, runs upward. Understanding this allows one to orient the blank in such a way as to carve to reveal the desired pattern.
While bowls are usually turned outside first, NIP is turned inside first to reveal the star pattern. Mount the blank on a faceplate, the faceplate on what will be the top or rim of the bowl, then round the blank and create a tenon. Before shaping the outside, reverse the piece onto the tenon and hollow it out to reveal the star pattern. Once this is completed, the outside can be turned. Reverse again to finish the bottom.
Tear out is significant with NIP end grain turnings. Being a neophyte turner, I have not figured out how to avoid or minimize this, though some use scrapers and others use various shaped gouges with better success than I have had—80 grit sandpaper and hours of time are making up for my turning inexperience. Any help in this area would be appreciated.
Ron Kent’s eponymous site www.ronkent.com has many tips regarding NIP and especially stabilization of this wood using an inexpensive 50:50 mix of liquid dishwashing detergent and water. I have found that Smart&Final carries a 5 gallon container of dishwashing detergent at a reasonable price. It is amazing how even a wet piece of NIP will soak up a large amount of this liquid, making subsequent turning quite wet. I have had luck turning the entire piece at one time, then applying several coats of oil, and had no cracks develop, but many advocate twice turning, or placing the once turned piece back in the detergent mixture or some other stabilization concoction. It amazes me how many ounces of tung oil the thirsty turned piece absorbs when oiled. Ron Kent would apply 50 or more coats in a several month process but he obviously had much more patience than I have.
Translucence can be achieved with a combination of a thin turning and how one finishes the piece. I will amend this post after I learn more about this—I have sent emails to a couple of the turners on this site asking how they achieved their NIP translucence—it seems to relate much to the finishing process and soaking of the piece in the appropriate mixture.
Another aspect of NIP is how easily it spalts, offering more unique and interesting patterns to a turning. I’ve read that if additional spalting is desired, some time in a moist environment before turning or in an inflated plastic bag is all that is needed.
While end grain turnings are often done with NIP, some spectacular pieces are created with side grain turnings—just review the 14 pages of NIP on this site to see some amazing work. The woodturning blanks site noted above also has a nice description of how to orient blanks to achieve desired results, including pictures that explain the tree anatomy and blank mounting better than I have written.
I have written this brief piece mainly to help me understand NIP and hopefully to engender some discussion so that I may learn more about this wood and end grain turning. Ron Kent’s turnings are what have inspired me—one of his beautiful bowls was purchased by me almost 40 years ago when in Hawaii—and still remains a favorite among my collection. I hope others will add to this thread and even correct my mistakes and comments.
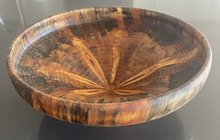
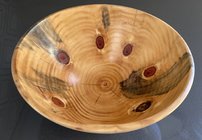
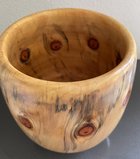
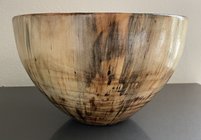
Last edited: