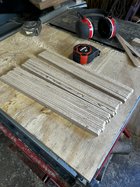
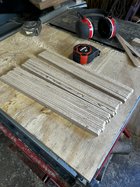
I imagine most of us keep the center slabs from sawing logs to remove the pith. I keep many of them anticipating small spindle work or short boards for flat work that can be made from these pieces, generally 15-18” long or shorter. In this case a piece of white oak wound up being perfect to get started making the 24 slats that form the umbrella portion of the swift. Here are a few pictures of my initial dressing of the board, jointing one edge and then cutting out three boards which I could run through my portable planer to make stock to take to the bandsaw for re-sawing.
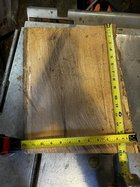
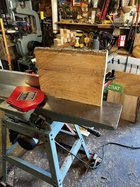
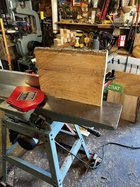