So my ladder falls and hits the (cheap) aftermarket regulator I have attached to my compressor and breaks the (accompanying cheap) connection pipe off flush with the compressor component leaving about 1/3" of threaded pipe inside the compressor component itself. If it would've broken on the regulator side I could just remove the rest of the pipe and replace the whole thing. But as it stands I'm gonna have to work the last bit of this male pipe out of the female threads. The pipe is copper so maybe that'll end up being to my advantage. How would you go about removing something like this? My camera takes bad close ups but to give some perspective the I.D. of the pipe is .40 in. Drew that line in there to show the end of the pipe.
I've got easy outs for rounded nuts but I'm not sure if there's anything like that for this situation. Can't be the first time it's happened to someone.
I'm afraid the pipe is in there fairly snug so I don't think prying one side up with a pic and then trying to work it around with some needle nose pliers is gonna get any kind of result.
I'm all ears. Thanks.
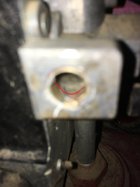
I've got easy outs for rounded nuts but I'm not sure if there's anything like that for this situation. Can't be the first time it's happened to someone.
I'm afraid the pipe is in there fairly snug so I don't think prying one side up with a pic and then trying to work it around with some needle nose pliers is gonna get any kind of result.
I'm all ears. Thanks.
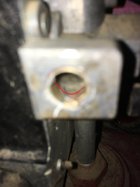
Last edited: