Hello - I'm looking to purchase my first wood lathe to make "ACORN" finials for a table I'm setting up for production. Looking for advice on how much Horse Power in a lathe I should get to efficiently turn these acorns. I'm thinking a mini or midi lathe. I'll probably make a dozen acorns at a time (not on the same blank, but twelve total). The acorns will be made of white oak. Any suggestions on how much H.P. I need? Thanks.
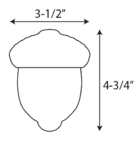
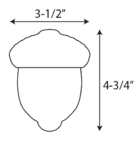