Hello everyone,
I'm Eric, a hobbyist woodworker in the SF Bay Area. Most of my work is with flat things (portfolio site: https://justwood.design/), but I got into spoon and then bowl carving a couple of years ago and really like those, in no small part because there's a community around it. They make great gifts and I enjoy the thrill of discovering what's inside a log when you split it open.
I took a class a few years ago on turning and liked it but didn't pursue. One of the guys in my carving group is a very accomplished turner and I realized that I had an opportunity to pursue it with some informal coaching. So, when a toolmaker - Wahuda - that I like (I own a jointer and planer from them) started making lathes, I waited until their second model emerged and went for it during their annual promotion, which included free shipping + lift gate as well as a free chuck.
I'm a buy once / cry once kind of person when it comes to tools, so I sprang for a really nice set of turning tools from Carter + Son based on advice on reddit and feedback from my friend. The pre- and post-sales experience have been phenomenal.
For sharpening, I went with a common setup: Rikon slow speed grinder, a 180 grit CBN wheel + wolverine. Craft supplies didn't have the kit with the raptor set up components. So I just copied my friend's using them as templates on a router table with a pattern bit and some 1/4" plywood. All of these things work well although I'm not really impressed with the build quality of the wolverine. I couldn't get the long bar past the cam and called Oneway who told me to grind off a corner. Really? Quality control? Also you have to jostle it so that it doesn't move when you lock it down -- this seems like a solvable problem, but they are the "default" so why bother.
I have a backlog of green wood that is getting less green and so rough turning those has been a priority. I will still carve bowls by hand too as I enjoy the quiet physicality of that. I'm experimenting with different ways to move drying along - I already had some desiccant beads and also tried boiling a couple of rough turned bowls. But I'm prepared to use the most effective tool, which is patience. I'm including a photo of the bench I made for the lathe. That sled hanging on the wall is no longer there as it's in the splash zone for green wood. I've hung a water proof poster-like thing in its place.
For fun I'm including a photo of a recent (hand carved) bowl as well as an interesting piece of plum crotch that I rough turned. That's enough for now I guess - I'm grateful that this forum exists and look forward to learning from others here.
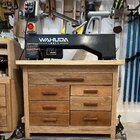
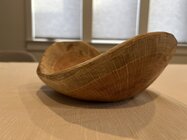
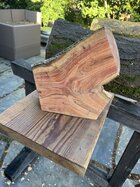
I'm Eric, a hobbyist woodworker in the SF Bay Area. Most of my work is with flat things (portfolio site: https://justwood.design/), but I got into spoon and then bowl carving a couple of years ago and really like those, in no small part because there's a community around it. They make great gifts and I enjoy the thrill of discovering what's inside a log when you split it open.
I took a class a few years ago on turning and liked it but didn't pursue. One of the guys in my carving group is a very accomplished turner and I realized that I had an opportunity to pursue it with some informal coaching. So, when a toolmaker - Wahuda - that I like (I own a jointer and planer from them) started making lathes, I waited until their second model emerged and went for it during their annual promotion, which included free shipping + lift gate as well as a free chuck.
I'm a buy once / cry once kind of person when it comes to tools, so I sprang for a really nice set of turning tools from Carter + Son based on advice on reddit and feedback from my friend. The pre- and post-sales experience have been phenomenal.
For sharpening, I went with a common setup: Rikon slow speed grinder, a 180 grit CBN wheel + wolverine. Craft supplies didn't have the kit with the raptor set up components. So I just copied my friend's using them as templates on a router table with a pattern bit and some 1/4" plywood. All of these things work well although I'm not really impressed with the build quality of the wolverine. I couldn't get the long bar past the cam and called Oneway who told me to grind off a corner. Really? Quality control? Also you have to jostle it so that it doesn't move when you lock it down -- this seems like a solvable problem, but they are the "default" so why bother.
I have a backlog of green wood that is getting less green and so rough turning those has been a priority. I will still carve bowls by hand too as I enjoy the quiet physicality of that. I'm experimenting with different ways to move drying along - I already had some desiccant beads and also tried boiling a couple of rough turned bowls. But I'm prepared to use the most effective tool, which is patience. I'm including a photo of the bench I made for the lathe. That sled hanging on the wall is no longer there as it's in the splash zone for green wood. I've hung a water proof poster-like thing in its place.
For fun I'm including a photo of a recent (hand carved) bowl as well as an interesting piece of plum crotch that I rough turned. That's enough for now I guess - I'm grateful that this forum exists and look forward to learning from others here.
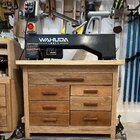
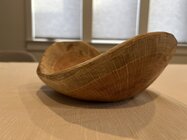
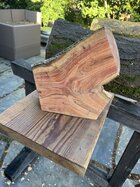