I've been working on putting together a drying box for rough turned bowls. Here are some pictures of the build and other details.
The non-working freezer was purchased via in online market forum. The cost was $100. There was no coolant present at the time of purchase. Due to space constraints, the kiln has to live outside. I made a brick platform for it to sit on for stability and to keep it off the ground to help prevent rust.
Box interior with shelving and rear baffle removed. Removed and discarded OEM low voltage fan. Installed 110v 210 CFM axial fan. Air flows to the rear of the box into a plenum. Air is diffused through the vent at the top
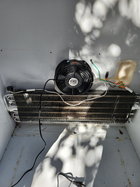
Baffle re-installed. Air is drawn through the bottom and side openings.
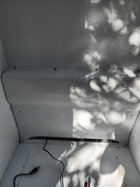
Hygrometer / Thermostat power distribution control. Fan is wired to the hygrometer, light bulb is wired to the thermostat. Set controls to run the fan until it drops below 10% RH. The light bulb runs until the temperature reaches 110. These are best guess initial settings. I would appreciate any thoughts on this based on your experiences.
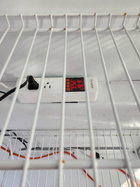
Temp/RH sensor installed at the top.
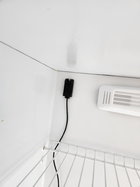
Continued in next post.
The non-working freezer was purchased via in online market forum. The cost was $100. There was no coolant present at the time of purchase. Due to space constraints, the kiln has to live outside. I made a brick platform for it to sit on for stability and to keep it off the ground to help prevent rust.
Box interior with shelving and rear baffle removed. Removed and discarded OEM low voltage fan. Installed 110v 210 CFM axial fan. Air flows to the rear of the box into a plenum. Air is diffused through the vent at the top
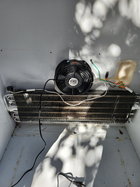
Baffle re-installed. Air is drawn through the bottom and side openings.
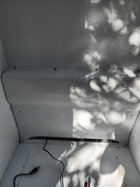
Hygrometer / Thermostat power distribution control. Fan is wired to the hygrometer, light bulb is wired to the thermostat. Set controls to run the fan until it drops below 10% RH. The light bulb runs until the temperature reaches 110. These are best guess initial settings. I would appreciate any thoughts on this based on your experiences.
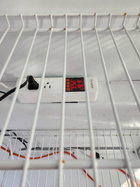
Temp/RH sensor installed at the top.
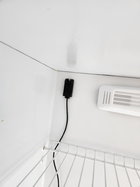
Continued in next post.