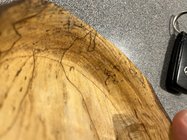
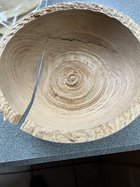
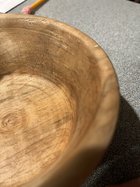
Lock your elbows to your body? You must turn all your bowls by standing at the end of the lathe. That lock your elbow advice dates back to the 50s when people were turning on crappy lathes with scrapers. The better advice is to dance with the work and move smoothly along. So far we have no idea what kind of tools his is using.for the first and last pictures, I seem to notice, for lack of better term, gouges in spots in the bowl - in my experience (limited as it is and still self-teaching) those happen when the bowl flexes, warps, or otherwise deviates from perfectly round (vibration of the bowl- perhaps not securely or properly chucked? in my case, my lathe has a bit of runout that I have to compensate for by very light cuts.. and Ive also gotten those when I got catches - the bowl walls flex a bit as the gouge catches... and for green wood (I.E. natural edge or once-turned) it happens when you don't get your inside form turned quickly enough - as the bowl loses moisture it starts to warp out of round) Those gouges can also happen from just trying to force a dull gouge into your wood (don't push the gouge into the wood, let the wood come to the gouge) as for the raggedy one in the middle, that looks like a few of mine that I first turned before I figured out what all those youtubers referred to as riding the bevel, and learned how to apply my pressure to the tool down into the tool rest instead of into the wood (lock elbows to sides and use your body to move the tool..) and lastly, I don't think your bowl split is from mis-judging wall thickness - looks to me more like there was already a crack in the wood (checks or ring shake?) that you caught with the tool, which at least for me almost always results in the bowl disintegrating into pieces unless I notice the cracking and do something to stabilize it first...
Yup, its what I do and no I dont turn at the end of the lathe - Granted your right elbow is further out, usually, when starting the cut down into the bowl, but your left elbow (and thus hand applying pressure down onto tool rest) can be locked down to your ribs , preventing you from trying to push your gouge into the cut - and still allows you to use your body movement (the turner's dance) to sway into the curves smoothly - You mention the dance - that is what it is - You do not use your arms, elbows, hands to move the tool - You use them to hold the tool in a position you want it and then your body movement (sway) does the moving - your body mass gives you far greater control. It took me quite a while to figure it out and then just really paying attention to how I was making the "good" cuts I find that it is because I am not moving my arms/hands (because elbows and tucked in to my ribs) and just using whole body (flexed knees and hips - sorta like learning your "sea legs" I guess) to control movement of the tool. (and BTW, what tool you are using should not matter - same principle applies - your hands just hold the tool in position, let the tool do the cutting, let your body control the movement)Lock your elbows to your body? You must turn all your bowls by standing at the end of the lathe. That lock your elbow advice dates back to the 50s when people were turning on crappy lathes with scrapers. The better advice is to dance with the work and move smoothly along. So far we have no idea what kind of tools his is using.
I do use a gouge with something like an Ellsworth grind, and thank you for the link!You never told us what types of tools you are using. If you use a bowl gouge with an Ellsworth grind, this video of David might help you out:
View: https://youtube.com/watch?v=wGupR8Lt9E0&feature=share
How thin are you going for?I've only been turning for about 3 years. At first, I didn't lose any bowls but that was mainly because I didn't attempt to get the walls too thin. I was just happy when they were smooth with no waves or tear out. Now that I've moved to attempting thinner walls, I've ruined a few bowls, but practice, constant checking of walls by feel in open bowls, and just being patient has made the losses less and less. The same is true with bowl bottoms. I don't like to just practice, preferring to create a finished product, but then the result is I lose some nice pieces. So I have started to practice on some junk, especially practicing getting the bowl walls to match the outside shape and be consistent in thickness; not too thin but thinner than I was doing. I am getting better slowly.
I do "practice" while roughing out a bowl, or taking a bowl towards the final thickness. Making every cut a good, clean cut gets you some practice - plus it gives you time to discover how that particular piece of wood is behaving, and what tools/techniques work and which don't.So I have started to practice on some junk, especially practicing getting the bowl walls to match the outside shape and be consistent in thickness; not too thin but thinner than I was doing. I am getting better slowly.
I just bought calipers after ruining a bowl. When I was doing smaller bowls there was no need for anything but visual inspection and touch. The larger bowls, I’ve realized are a bit more difficult. The inside is smooth but, on a couple of bowls recently I got just one area to thin because it didn’t follow the outside shape. Just a matter of learning what I should check more often. I would be happy if the walls were around a 1/4” unless the design indicates a more substantial or thinner wall. My technique with the gouge has improved a lot, especially after a class with Trent Bosch last fall. i have another this spring unless COVID interferes. There‘s nothing that improves your skills and technique more then doing nothing but turning for 3 or 4 days (although it is exhausting too).How thin are you going for?
I use calipers - lets me now the wall thickness rim to the Chuck which gives a close measure of the bottom thickness.
Been at it over 30 years and never go through the wall or bottom.
On all bowls I set the rim thickness first bye eye and use that for the rest of the wall thickness
I set the calipers with a little gap. Hold one side on the inside wall and run them down the wall.
I often put my finger tip under the tip of the caliper as I run it down the wall this lets me see where it needs to be cut when I feel a pinch on my finger tip.
On traditional bowls I let the wall thickness decrease slightly from the rim to the bottom.
On NE bowls 12-16” I do a wall thickness 3/16” to 5/16 keeping it even rim to bottom
On smaller NE bowls I go for a wall thickness 1/8” to 3/16”
On the NE bowls every once in a while the calipers will tell me I have cut too thin so I pick up the cut at the proper thickness whinch leaves a tiny ridge that I blend in sanding. Continuing to cut on the too thin cut line just makes the wall thinner.
Roughing a bowl does improve skills with a gouge but there’s nothing like just taking a piece of wood that is nothing special and repetitively doing what you are having problems with. I have no interest in practicing on a special piece of wood.I do "practice" while roughing out a bowl, or taking a bowl towards the final thickness. Making every cut a good, clean cut gets you some practice - plus it gives you time to discover how that particular piece of wood is behaving, and what tools/techniques work and which don't.
Also, I aim for a consistent wall thickness starting at maybe 3x or more of my final wall thickness I'm going for. Get the wall consistent/even all the way down while it's still thick, matching the outside shape. Then, on those cuts getting down to your final thickness you just take off an even amount with each pass (watching the depth of the ridge you are making). You'll end up with a consistent wall after each consistent pass. So you can stop worrying so much about wall thickness, breaking through, etc, and just concentrate on good cuts.
Trent is a terrific instructor. Our techniques are are quite similar but we do some things differently.I just bought calipers after ruining a bowl. When I was doing smaller bowls there was no need for anything but visual inspection and touch. The larger bowls, I’ve realized are a bit more difficult. The inside is smooth but, on a couple of bowls recently I got just one area to thin because it didn’t follow the outside shape. Just a matter of learning what I should check more often. I would be happy if the walls were around a 1/4” unless the design indicates a more substantial or thinner wall. My technique with the gouge has improved a lot, especially after a class with Trent Bosch last fall. i have another this spring unless COVID interferes. There‘s nothing that improves your skills and technique more then doing nothing but turning for 3 or 4 days (although it is exhausting too).