My dust extraction is by Camvac-4” down to 2-1/2” at the lathe. It’s only used for sanding as the centrifugal force of the shavings means it only catches a small amount. At the lathe end of the semi rigid flexible pipe is a 6” x 3” mouth.
In another life I play with LBCs and carburettored engines. It’s accepted that nicely rounded inlet ports improves breathing.
Would it improve the dust collection if I machined a circular “mouth” with rounded edges? My instinct tells me that trying to cover more of the work with the 6” width is not helping.
Or am I fussing over something that won’t make much difference?!!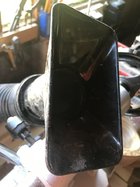
In another life I play with LBCs and carburettored engines. It’s accepted that nicely rounded inlet ports improves breathing.
Would it improve the dust collection if I machined a circular “mouth” with rounded edges? My instinct tells me that trying to cover more of the work with the 6” width is not helping.
Or am I fussing over something that won’t make much difference?!!
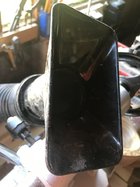