I've been asked to make some handles for a woodworking vise.
Here is the handle to be copied:
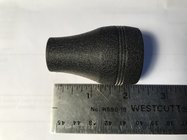
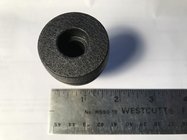
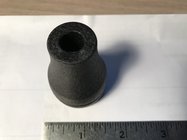
Here is the stock I was supplied.
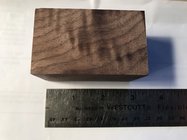
As the title says. my question is about workholding.
The through hole makes me think my best best is drilling the through hole and counter bore and then putting it on a mandrel.
I don't have a mandrel though I suppose a bolt of the correct diameter would work. If I use a mandrel then the only think I can think of is to stick my MT2 drill chuck in the headstock and hold the shaft of the bolt in the chuck. Except we all know that drill chucks have terrible runout.
To hold the blank in the chuck, I would have to get smaller capacity jaws. If I did get smaller jaws, I think I'd drill it, make the counterbore, turn it round then make the shape and part it off. Or just leave it in the orientation and make the narrow part be nearest the chuck.
But I'd really like some expert perspectives as I'm a bit nervous about doing this job. The workbench the handles are for is a woodworking tour de force, absolutely beautiful and I feel a bit like a hack because I've never done anything like this before :O
Here is the handle to be copied:
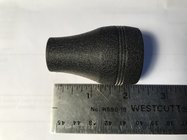
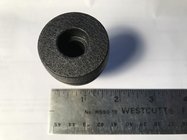
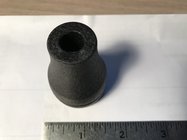
Here is the stock I was supplied.
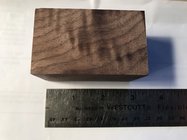
As the title says. my question is about workholding.
The through hole makes me think my best best is drilling the through hole and counter bore and then putting it on a mandrel.
I don't have a mandrel though I suppose a bolt of the correct diameter would work. If I use a mandrel then the only think I can think of is to stick my MT2 drill chuck in the headstock and hold the shaft of the bolt in the chuck. Except we all know that drill chucks have terrible runout.
To hold the blank in the chuck, I would have to get smaller capacity jaws. If I did get smaller jaws, I think I'd drill it, make the counterbore, turn it round then make the shape and part it off. Or just leave it in the orientation and make the narrow part be nearest the chuck.
But I'd really like some expert perspectives as I'm a bit nervous about doing this job. The workbench the handles are for is a woodworking tour de force, absolutely beautiful and I feel a bit like a hack because I've never done anything like this before :O
Last edited: