Can't match your experience with purpleheart, I do recall dry Madrone and dry chestnut were extremely difficult (but with novice status, that doesn't mean much). Just want to throw out there, I overheard a couple of bowl turners discussing how much lathering up a difficult dry bowl blank with soap and water makes the cutting much easier. Haven't tried it m'self.
The purpleheart bowl that inspired this thread was completed yesterday (except for the foot), I had such a difficult time with the last one, that I did a fairly easy shape that lent itself to easy sanding.
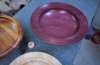
Today, I'm working on a new problem bowl......black and white ebony. I have turned a couple Gabon ebony bowls in the past, but l haven't ever turned black and white ebony. It's not similar at all.....!
This piece of wood was very expensive, and I don't want to take any chances experimenting with unknown techniques. It wasn't all that difficult to get a reasonable cut when it was wet. Now that it's stabilized, it's being very difficult to get a decent cut. I'm a little hesitant to use soap and water on it, because I'm not sure how to remove soap, once it is introduced into the wood. Maybe you could ask your turning friends just how they deal with this.......?
I worked on this again this afternoon, and came up with a better surface than you see here, but still not as good as I'd like prior to sanding.
Unfortunately, this black and white ebony roughout developed a severe crack during seasoning, and will need an epoxy repair. I'm not sure I can sell this one, because the split is pretty obvious (not shown in this photo).......darn it!

Even though there is a serious flaw, I want to finish this one as best as I can......for the experience of it. It was such a disappointment to see the split. :mad:
I was warned by the seller of this block that black and white ebony is known for splitting badly......anyone want to comment on that? Has anyone else made a bowl out of black and white ebony before?

ko