Several have expressed some interest on what has become a long-term project. It came out of the coating booth today with first round clearcoat. Next step is 800-grit sanding around the openings and then taping for sand-blast. The purpose of that is to remove finish from those areas that can't be sanded.
The clearcoat creates a "high-gloss" which, to my thinking, is not attractive. After the sandblasting, it will be sanded w 800 and then clearcoated again.
Then final rub-out. I'll start with an 800-grit paper back (Eagle yellow) which will eliminate all orange-peel. Then I'll proceed with Assilex 1000, 1500, 2000, 3000 and then compound for a "high-lustre" surface. You can get the Eagle abrasive from Turningwood.com.
While I will use a 3/32 DA sander for the 800, I'll hand sand the Assilex. Even on this big piece, it is faster. It's kind of a kick to dry sand by hand out to 3000 - you can actually hear the stuff cutting - I couple or three swipes and move on.
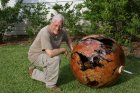
The clearcoat creates a "high-gloss" which, to my thinking, is not attractive. After the sandblasting, it will be sanded w 800 and then clearcoated again.
Then final rub-out. I'll start with an 800-grit paper back (Eagle yellow) which will eliminate all orange-peel. Then I'll proceed with Assilex 1000, 1500, 2000, 3000 and then compound for a "high-lustre" surface. You can get the Eagle abrasive from Turningwood.com.
While I will use a 3/32 DA sander for the 800, I'll hand sand the Assilex. Even on this big piece, it is faster. It's kind of a kick to dry sand by hand out to 3000 - you can actually hear the stuff cutting - I couple or three swipes and move on.
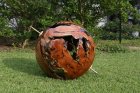
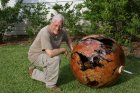