Hello to all fellow woodturners. I'm hoping either you, or you know someone who can help/direct me how to solve my VFD problem.
I have a used Delta 46-745 with the 110v, 1.5hp motor. I bought it used as a backup/fixer upper. And of course as a used lathe the major problem is in the electrical side of the house. By the way I'm a civil engineer who tries to stay as far away from electricity but gets drawn back in nonetheless.
When you start the lathe the speed seems to build slowly and when you engage a tool for example in bowl turning, the speed slows and shortly the lathe quits and the power and fault lights blink. You can restart it after a few minutes of rest. I took the motor to a "motor" shop and they applied 220v, which is what the motor requires, and it seemed to turn freely. So my deduction is that the problem is in the VFD.
Any ideas how to troubleshoot
this? Should I just replace the VFD and if so what's your recommendation on brand and model, of course based on our common interest of doing it as "inexpensively" as possible.
Thanks so much - Finn Posner
I have a used Delta 46-745 with the 110v, 1.5hp motor. I bought it used as a backup/fixer upper. And of course as a used lathe the major problem is in the electrical side of the house. By the way I'm a civil engineer who tries to stay as far away from electricity but gets drawn back in nonetheless.
When you start the lathe the speed seems to build slowly and when you engage a tool for example in bowl turning, the speed slows and shortly the lathe quits and the power and fault lights blink. You can restart it after a few minutes of rest. I took the motor to a "motor" shop and they applied 220v, which is what the motor requires, and it seemed to turn freely. So my deduction is that the problem is in the VFD.
Any ideas how to troubleshoot
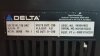
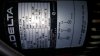
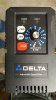
Thanks so much - Finn Posner