Part of a big "burl" I got 2 weeks ago. Cut out a piece
Left in shavings 2 weeks and started to tackle tonite. These cracks have not gone far at all. I have seen this years ago in maple. Such a pretty wood piece,-hated to give up.
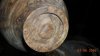
Have superglued some of the "cracks (some are not "real" )tonite and wonder if it's worth the risk tomorrow to continue. Such a pretty piece of wood!!!!!.
Left in shavings 2 weeks and started to tackle tonite. These cracks have not gone far at all. I have seen this years ago in maple. Such a pretty wood piece,-hated to give up.
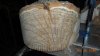
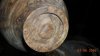
Have superglued some of the "cracks (some are not "real" )tonite and wonder if it's worth the risk tomorrow to continue. Such a pretty piece of wood!!!!!.