Most turners know better than to use sheetrock screws when mounting wood to a faceplate. Ive also had my share of deck screws snap off on me.Then I found a box of screws at Home Depot that looked like a better choice, concrete screws. The brand I found is Tapcon by ITW Brands. The minimal shear strength listed on the box was over 700 lbs and the pullout from concrete about 350 lbs. So far these this have been pretty well bomb proof.
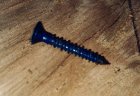
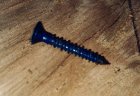