My late friend made up set-up blocks that would lay on the bed so that the base of the Easy-Core could be set at the correct distance from the headstock to produce a standard bowl base thickness. Since there are 3 knives, you basically need 3 block sets, but in order to make it more flexible, he cut a variety of thinner blocks of 1/2-1.5" that could be added together to make the desired thickness. The cost is only your time, as you're using scrap wood for the blocks, no giant notebook needed. He made his from particle board shelf remnants, which allows them to be labeled with a sharpie.
You create the set-up with no blank mounted, by positioning the Easy-Core base so that the knife cuts to the desired depth (distance from the face of the jaws) at or near centerline, and measure that distance from the base of the Easy-Core to the headstock, for each of the 3 knives. Make a block that is the smallest of the distances, the "starter block", and use the "shims" to create the distance needed for each knife. You can also vary the distance by small amounts by swapping "shim" blocks to make the bowl bottom thickness more or less than standard. If you change chucks or change jaws, you'll have to adjust the set up, because changing those will change the distance from headstock to jaw face. (In my system, which now that I look at it is very messy and confusing, I've written those distances for different chuck/jaw combos on the "starter block".)
In use, it's 1) mount the blank into the chuck 2) on the lathe bed, put the appropriate blocks for the knife you want to use 3) slide the Easy-Core base up to the block, and voila', your depth is set. With the base against the positioning block, you then adjust the base position so that the knife starts the cut at the desired wall thickness, lock it down and go to work.
This is much easier to understand visually, than in words:
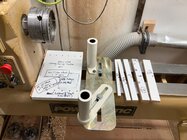
In use, one or several of the thin blocks would be placed between starter block and OneWay base. (Note that the 3520A lathe has a slightly curved edge to the headstock base, so the starter block is made to allow for it)