I have a question for you vastly more experienced turners. I'm seeing a lot of what I'm calling micro tear out. Maybe it is just tear out but it seems pretty fine yet stubbornly hard to get rid of.
First off, I'm using a 55º swept back bowl gouge and yes I kiss it before the final cuts with a 180 grit CBN wheel. I'm "ridding the bevel" as much as I can and keeping the last several cuts very light. Sometimes I sheer scrape too using the bowl gouge or a slightly rounded skew chisel.
This tear out I'm seeing really bad in second turnings of very dry Cherry, Maple and Walnut. But it seems easier to sand out of the Walnut. I watched several good videos on YouTube referencing this but despite my efforts its still there in many of my bowls.
Is it the species of wood I'm using?
Am I just being too picky?
Is sanding the crap out of these hardwoods normal?
Thanks for thoughts and comments in advance. Have a great Memorial Day!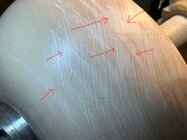
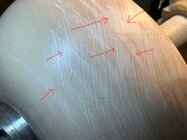
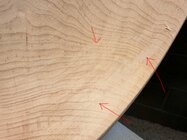
First off, I'm using a 55º swept back bowl gouge and yes I kiss it before the final cuts with a 180 grit CBN wheel. I'm "ridding the bevel" as much as I can and keeping the last several cuts very light. Sometimes I sheer scrape too using the bowl gouge or a slightly rounded skew chisel.
This tear out I'm seeing really bad in second turnings of very dry Cherry, Maple and Walnut. But it seems easier to sand out of the Walnut. I watched several good videos on YouTube referencing this but despite my efforts its still there in many of my bowls.
Is it the species of wood I'm using?
Am I just being too picky?
Is sanding the crap out of these hardwoods normal?
Thanks for thoughts and comments in advance. Have a great Memorial Day!
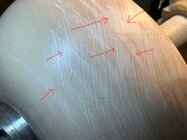
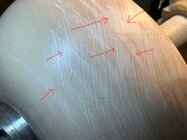
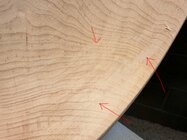