Finally decided to get off my duff and make an offset fixture to hold a sphere and put some design into it. While I've done some between centers offsetting before, that just allows me to put lines in 1 direction or axis. This jig allows to rotate the sphere and crisscross the line. This is no David Reed Smith level jig but it did work well and will hold a 2.75" to 4" sphere without any adjustments.
Took a couple rubber chuckies that I wasn't using and attached them to a 3/4 x 10 bolts that were epoxied into a couple pieces of scrap wood I had laying around. Offset for this style is 3/4". Took another scrap piece and tapped the 3/4 x 10 hole for the tailstock and then attached that piece to the bolt piece.
Tried it out on a cherry piece that I had previous done and put 3 splits into the piece that where perpendicular to the existing splits. I was pretty satisfied with (no picture) the results so I tried to put a few more cuts into the piece at a 45 degree angle.........well that didn't work out so well. Not sure if it was because of grain direction or maybe trying to feed a little to fast but I lost the point of the vortex tool and got a little section chip out.
Dressed up the tip of the tool a bit (still need a little better point) and tried it out on an oak sphere. Nice clean cuts so I'm satisfied with the 1st trial runs. Have to say I was a little worried and had a little pucker factor spinning a 4" ball at 1,000 rpm's but after it was done, I'd say if the piece wasn't as secure as it was the cut quality wouldn't be there.
Thinking about masking off the sphere and then cutting and then maybe spraying a color into the splits. Here's a couple pics of today's adventure.
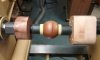
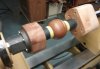
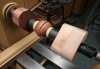
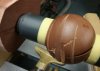
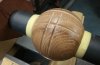
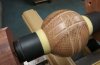
Took a couple rubber chuckies that I wasn't using and attached them to a 3/4 x 10 bolts that were epoxied into a couple pieces of scrap wood I had laying around. Offset for this style is 3/4". Took another scrap piece and tapped the 3/4 x 10 hole for the tailstock and then attached that piece to the bolt piece.
Tried it out on a cherry piece that I had previous done and put 3 splits into the piece that where perpendicular to the existing splits. I was pretty satisfied with (no picture) the results so I tried to put a few more cuts into the piece at a 45 degree angle.........well that didn't work out so well. Not sure if it was because of grain direction or maybe trying to feed a little to fast but I lost the point of the vortex tool and got a little section chip out.
Dressed up the tip of the tool a bit (still need a little better point) and tried it out on an oak sphere. Nice clean cuts so I'm satisfied with the 1st trial runs. Have to say I was a little worried and had a little pucker factor spinning a 4" ball at 1,000 rpm's but after it was done, I'd say if the piece wasn't as secure as it was the cut quality wouldn't be there.
Thinking about masking off the sphere and then cutting and then maybe spraying a color into the splits. Here's a couple pics of today's adventure.
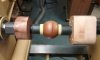
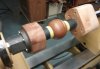
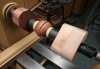
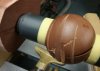
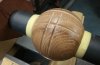
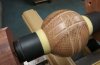