I'm turning several koa logs at present - lots of surprises and issues to deal with. But living here in Redneck, TX you don't just walk out and cut yourself a koa tree - I was lucky to get several logs and, in spite of the issues, turn them I will.
An odd design is a face turning on a tall vase - I was forced into it due to the cut of the log. The log was cut just below the crotch. So...I got it shaped and found the crotch extended so that it went completely through the piece. No way would this withstand hollowing. What to do?
Solution (hopefully) - I applied splints with West Epoxy G-Flex. I plan to hollow later this week. Then, after it dries over the next 8-months, I'll do a permanent fix with the G-Flex, turn off the splints, do the final turning and finish. My thinking is the dark-brown epoxy fix will enhance the value.
A few years ago I fixed a mesquite vase (also attached) with a wind shake that went all the way across - found it when I was hollowing - had to go change shorts. Fixed it with G-Flex and it's in somebody's home.
Will be happy to respond to anyone that wants to know a bit more about G-Flex - unlike most epoxies, it adheres to wet wood (wooden boat guys use it for wet wood repairs) - it has been a valuable tool over the years.
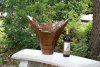
An odd design is a face turning on a tall vase - I was forced into it due to the cut of the log. The log was cut just below the crotch. So...I got it shaped and found the crotch extended so that it went completely through the piece. No way would this withstand hollowing. What to do?
Solution (hopefully) - I applied splints with West Epoxy G-Flex. I plan to hollow later this week. Then, after it dries over the next 8-months, I'll do a permanent fix with the G-Flex, turn off the splints, do the final turning and finish. My thinking is the dark-brown epoxy fix will enhance the value.
A few years ago I fixed a mesquite vase (also attached) with a wind shake that went all the way across - found it when I was hollowing - had to go change shorts. Fixed it with G-Flex and it's in somebody's home.
Will be happy to respond to anyone that wants to know a bit more about G-Flex - unlike most epoxies, it adheres to wet wood (wooden boat guys use it for wet wood repairs) - it has been a valuable tool over the years.

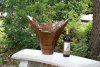