That is a very interesting setup Rich. I am assuming the lathe itself "rocks" and not the tool. Does anyone know of plans that would have the tool rock? I am not too keen on having my Oneway 2436 rock like that Midi Delta.
Marshall,
Indeed, the lathe itself rocks. That is the "aha" I took away from Richard Coer's design. I was initially planning to go down the path you are describing with my PowerMatic 3520B. I exchanged eMails with Jon Magill (one of the leading thinkers in the ornamental lathe community) about this, and he told me to look at how the Paul Cler lathe had worked. A picture of that lathe is below :
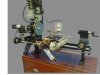
The other option is to go with a CNC-based one like being done by Bill Ooms (
http://cornlathe.billooms.com/index.html).
I decided to go with a smaller approach first. There are basically three options here :
- Build an MDF rose engine lathe that was designed by Jon Magill (and published in the AAW magazine, or you can go to http://www.whidbeyworks.com/root/MDF_Rose_Engine.html). That is where Michael is going (the guy who started this thread).
- Use a small lathe like Richard Coer outlined (and I modified in the approach I've taken).
- Go whole hog into this with a new rose engine lathe. There are a number out there, but the one that seems to come up most in the publications I've seen is the Lindow rose Engine (https://lindowmachineworks.com/lindow-rose-engine-menu/). (Or ... if you REALLY want to get fully into this, go for the MADE lathe {https://madelathe.com/}).
I wanted to see how much I liked ornamental turning before I sunk a lot of $ into it. The 1st or 2nd option met my needs. I chose the 2nd approach as I wasn't too keen on the way the MDF rose engine shaft wasn't rotating on bearings. Not discounting the MDF approach as it has been thoroughly vetted by many, just wasn't my cup of tea.
As it is, I also ended up making a bit of my own parts, including the cutting frame. The data on Bill Ooms' site helped greatly.
But there is still a lot you have to figure out on your own. Things like overhead drives for the cutting frame. And, overall, there is not much help out there -- including on the Ornamental Turners site. I joined and wasn't able to get help anywhere near what I see on this forum. So I'm glad I took this intermediate step first.
I have some ideas fleshed out on how to take a Paul Cler approach for adding this to my 3520B. Probably will pursue it in a year or two.
Bill Ooms' approach of using CNC has some really cool advantages; however as an IT professional (for work), I'm not too keen on getting into a hobby where I have to maintain computer systems for the rest of my life. Want things to be easier.
The mechanical approach (using cams) requires some maintenance, but it is easier to see and diagnose (for me). I'll probably continue going down that path.
If you want to go down the path of ornamental turning, I do encourage you. It is fun and you can make some really cool stuff. Here's one I made from a small piece of desert ironwood. Just a little bowl for my bride to use for M&Ms snack (1 3/8" x 2 1/5").
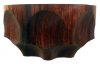
If you would like to learn from what I've done, PM me. I'll be glad to chat and tell you what worked for me, and what didn't.
Kind regards,
Rich