I have used the vinegar with steel mixture a few times, nothing special to it, the same with the ammonia treatment.
I never washed the steel wool, as the oil will float on the surface and is easily skimmed off.
The biggest problem is the tannin that is or is not in the wood and how much and how even in the different pieces, even from the same tree/log, not easy to find out without trial of small offcuts.
Wood without tannin or very little can be treated with tannin, strong thee does increase the tannin, and you can get tannin on-line, it is used by leather production and hides treatment, I have never used any of that.
My use was with some Red Oak turnings and also Apple and Honey Locust, I do have some pictures of the Oak and one of the Apple piece, none of the Honey Locust or the Fuming, that was all before we had digital picture taking.
The fuming was done with fresh household Ammonia, a flat plastic dish for the Ammonia and a tent made out of some plastic sheet over the turning and the Ammonia, left for two days I think I did, the color is much more brown than the vinegar and steel wool, as that has a blueish sheen to it, the Apple wood was colored more evenly as the year rigs and early/late wood are not like in the Oak or the Honey locust
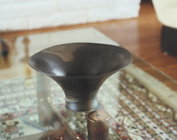