I think it was @John K Jordan who, in a recent thread, described putting a taper on a small piece of wood to insert it right into the headstock spindle taper to skip using a chuck for small spindle work. I've forgotten about this method, been a long time... A machinest website found me this table of morse taper dimensions-
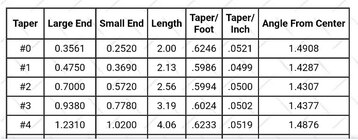
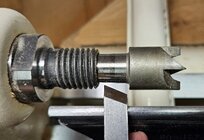
So I'm going to regrind a forgotten Sears skew chisel to a new angle (1.43 degree, or whatever is humanly possible freehand). When I want to insert a small piece of wood right into the spindle taper, I'll eyeball the toolrest parallel to the bed ways, eyeball the tool square to the toolrest, and scrape a half inch or so of taper onto the wood spindle. This should take most of the guesswork out of cutting a taper get a reasonably good taper fit of the wood into the spindle, and a little tailstock pressure (not mallet pounding like I've seen demonstrated, poor bearings!) will set the wood into the drive spindle taper.
Thanks for reminding me of this method, John (if that was you).
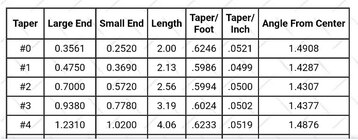
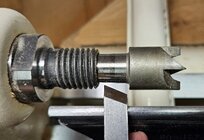
So I'm going to regrind a forgotten Sears skew chisel to a new angle (1.43 degree, or whatever is humanly possible freehand). When I want to insert a small piece of wood right into the spindle taper, I'll eyeball the toolrest parallel to the bed ways, eyeball the tool square to the toolrest, and scrape a half inch or so of taper onto the wood spindle. This should take most of the guesswork out of cutting a taper get a reasonably good taper fit of the wood into the spindle, and a little tailstock pressure (not mallet pounding like I've seen demonstrated, poor bearings!) will set the wood into the drive spindle taper.
Thanks for reminding me of this method, John (if that was you).