Mark Hepburn
Artist & Chef
Hi Everyone.
So I did this bowl in elm with a segmented band around the middle. Aside from my dissatisfaction with the clunkiness of the form and the finial, there's this finish issue that I couldn't resolve so I just forged ahead.
NONE of this showed up during turning. I went through the grits from my old faithful 100 to 600. Wiped with tack cloth and mineral spirits and let dry. Top coated with spray poly. The first coat this appeared and so I waited, then re-sanded and finished again. Same result.
I decided to try again so i did and this time I hit it with mineral spirits again and no tack cloth and let it sit a few days before recoating. Then did a "seal coat" with dewaxed shellac (fresh Zinsser universal seal coat) before putting on poly. The final result is what you see.
I've done a lot of flat work over the years and so my first thought was that my prep was insufficient but then, I've never worked with some of the woods I've turned when doing cabinets, etc.
Any help anyone can offer would be very welcome.
Thanks!
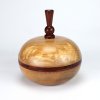
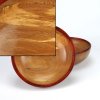
So I did this bowl in elm with a segmented band around the middle. Aside from my dissatisfaction with the clunkiness of the form and the finial, there's this finish issue that I couldn't resolve so I just forged ahead.
NONE of this showed up during turning. I went through the grits from my old faithful 100 to 600. Wiped with tack cloth and mineral spirits and let dry. Top coated with spray poly. The first coat this appeared and so I waited, then re-sanded and finished again. Same result.
I decided to try again so i did and this time I hit it with mineral spirits again and no tack cloth and let it sit a few days before recoating. Then did a "seal coat" with dewaxed shellac (fresh Zinsser universal seal coat) before putting on poly. The final result is what you see.
I've done a lot of flat work over the years and so my first thought was that my prep was insufficient but then, I've never worked with some of the woods I've turned when doing cabinets, etc.
Any help anyone can offer would be very welcome.
Thanks!
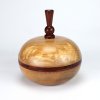
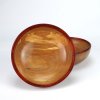
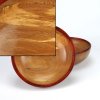
Last edited: