... I don't want to dance any more. I trying to find our what to use to keep my PM from dancing when I turn off centered work. I typically use 1 1/2" x 12" x 12" soft maple, faceplate mounted and I move my 4" FP to different positions on the back of stock to create different center points of turning. See the attached finished work to get an idea of what I turn.
My first attempt was to add a shelf and 6- 60lbs bags of sand. I have the 18" bed extension in the lower position and the head stock moved all the way to the end to utilize a larger diameter wood. I love this feature for this type of work. Anyway in this situation I could only get about 425rpm with our shaking the crap out of the lathe when I moved the face plate to and off center location.
The second attempt was to remove the sand bags and bolt the lathe to the floor by placing an 1/2" x 2" x 23+" steel bar drilled to slip over the top of the levelers and then bolted the bar to the the floor on each end, using 4- 1/2" x 6" weage bolts. Since my floor was not level I ended up screwing the levelers down about an inch and a half from the base of the leg, big mistake. I thought I was all set..put my off center work on the head stock and slowly brought up the speed. At about 530rpm I was back at doing the dance, and I am now left with 2 bent leveling legs and a lathe that has its mind set on dancing.
Any ideas or thoughts...Thanks
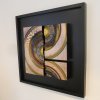
The second attempt was to remove the sand bags and bolt the lathe to the floor by placing an 1/2" x 2" x 23+" steel bar drilled to slip over the top of the levelers and then bolted the bar to the the floor on each end, using 4- 1/2" x 6" weage bolts. Since my floor was not level I ended up screwing the levelers down about an inch and a half from the base of the leg, big mistake. I thought I was all set..put my off center work on the head stock and slowly brought up the speed. At about 530rpm I was back at doing the dance, and I am now left with 2 bent leveling legs and a lathe that has its mind set on dancing.
Any ideas or thoughts...Thanks