Hollowing has been underway for almost a month and finally got to self bail - that's when I cut through a deep bark inclusion on the side and open a hole for the shavings to come out - no more blowing or raking out.
The 3rd pic on the right shows the log on the steady rest - to the right I cut out the shrink-wrap at the first deep bark and you can see the cut-through. I put the camera up to the hole (2nd pic) to show the terracing pattern used to hollow - seems that the Rolle Munro is more efficient pushing into the grain than side swiping. For rough-hollowing I use the HSS cutters - carbide will not withstand the abuse.
Hopefully in the next week I'll have a longer tool rest made that will go deeper into the vessel - extending 10"+ over the small rest is a bit dicey.
I added 300-lbs of ballast but still can't seem to get much over 150-rpm. While it will never be close to balanced, I hope to get to 200-rpm when the mass goes down under 400-lbs.
Best "wag" is it is 10% hollowed - shavings from hollowing is a bit over 55-gallons.
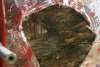
The 3rd pic on the right shows the log on the steady rest - to the right I cut out the shrink-wrap at the first deep bark and you can see the cut-through. I put the camera up to the hole (2nd pic) to show the terracing pattern used to hollow - seems that the Rolle Munro is more efficient pushing into the grain than side swiping. For rough-hollowing I use the HSS cutters - carbide will not withstand the abuse.
Hopefully in the next week I'll have a longer tool rest made that will go deeper into the vessel - extending 10"+ over the small rest is a bit dicey.
I added 300-lbs of ballast but still can't seem to get much over 150-rpm. While it will never be close to balanced, I hope to get to 200-rpm when the mass goes down under 400-lbs.
Best "wag" is it is 10% hollowed - shavings from hollowing is a bit over 55-gallons.
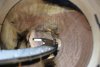
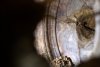
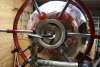
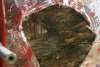