Photogrammetry involves creating accurate 3D models from a series of computer processed digital photos of an object.
I've done architectural restoration, this method makes it possible to accurately duplicate a detail without having to measure or take it with me. An object up on a building could be done with a telephoto lens. The photogrammetry software uses camera calibration to determine object size.
All sorts of possibilities in the art field. Seems more and more artists are no longer doing their complete pieces, only providing a small clay model to be scanned and built up to size. 3D models can be 3D printed for investment casting. High dollar pieces could advertised with a rotatable picture for viewing from all angles.
There are hand held scanners to do this same thing, pricing a few years ago was "if you have to ask you can't afford it" category. Prices are coming down, still in the $5K to $10K area. This method only needs a digital camera or smartphone.
The first picture shows a 5" tall "turning" as an example. 40 some photos were taken in a light box by rotating the part on a turntable. If an item is too big to move it can be done by walking around it while the photos are taken.
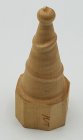
The photo set was uploaded to 3D Zephir software (there's a free version). My medium speed computer cranked away for half an hour, this next picture shows the result ready to export in a variety of CAD and graphic formats depending on the intended use. The computer processing time appears to go up exponentially with the number of photos. 500 photos could most of a day on a slow computer. Having an nVidia graphics processor speeds the processing up substantially.
Getting a usable photo set can be frustrating at first. The first 10 minutes of processing this photo set involved analysis to determine which ones were acceptable, a couple were rejected. You need good quality, non blurry pictures, lighting is critical. The software requires any given spot on the object to be shown in at least 3 pictures which makes overlap in the series important. Really frustrating and time wasted to have only 4 out of 60 be acceptable, BTDT, a couple too many times.
I exported the 3D model in a CAD format. This screen shot from my CAM software shows the part after "turning" on a 4 axis miling machine. The part could have been scaled in this step, bigger/smaller,taller/shorter, skinny/fatter. Or, that can be done on the machine.
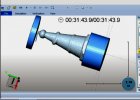
If you're at all interested, give it a try. Download the software,3D Zephyr, either free or standard version for 14 day trial. There's a photo set in their first tutorial that can by used. Some of you are good photographers, you might want to make your own set.
I've done architectural restoration, this method makes it possible to accurately duplicate a detail without having to measure or take it with me. An object up on a building could be done with a telephoto lens. The photogrammetry software uses camera calibration to determine object size.
All sorts of possibilities in the art field. Seems more and more artists are no longer doing their complete pieces, only providing a small clay model to be scanned and built up to size. 3D models can be 3D printed for investment casting. High dollar pieces could advertised with a rotatable picture for viewing from all angles.
There are hand held scanners to do this same thing, pricing a few years ago was "if you have to ask you can't afford it" category. Prices are coming down, still in the $5K to $10K area. This method only needs a digital camera or smartphone.
The first picture shows a 5" tall "turning" as an example. 40 some photos were taken in a light box by rotating the part on a turntable. If an item is too big to move it can be done by walking around it while the photos are taken.
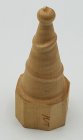
The photo set was uploaded to 3D Zephir software (there's a free version). My medium speed computer cranked away for half an hour, this next picture shows the result ready to export in a variety of CAD and graphic formats depending on the intended use. The computer processing time appears to go up exponentially with the number of photos. 500 photos could most of a day on a slow computer. Having an nVidia graphics processor speeds the processing up substantially.
Getting a usable photo set can be frustrating at first. The first 10 minutes of processing this photo set involved analysis to determine which ones were acceptable, a couple were rejected. You need good quality, non blurry pictures, lighting is critical. The software requires any given spot on the object to be shown in at least 3 pictures which makes overlap in the series important. Really frustrating and time wasted to have only 4 out of 60 be acceptable, BTDT, a couple too many times.
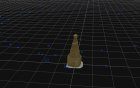
I exported the 3D model in a CAD format. This screen shot from my CAM software shows the part after "turning" on a 4 axis miling machine. The part could have been scaled in this step, bigger/smaller,taller/shorter, skinny/fatter. Or, that can be done on the machine.
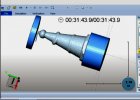
If you're at all interested, give it a try. Download the software,3D Zephyr, either free or standard version for 14 day trial. There's a photo set in their first tutorial that can by used. Some of you are good photographers, you might want to make your own set.