This thread has brought up a couple of points that I’d like to comment on from
my perspective. Obviously others have different circumstances and have their own views.
First off though, I’ve actually dug out my O’Donnell and found they are probably an intermediate model? I believe early ones were simpler with no facility for adding inserts. Mine however are marked as 2” and have holes to add inserts and have a black oxide? Finish of some sort. Current models are made from stainless steel in metric sizes, 50mm, 38mm and 25mm. Plus inserts for the largest model.
These are mine.
Some musings. I have six or seven chucks for both metal work and wood turning lathes. The Axminster SK100 I have is without doubt one of the best quality chucks I have. The only one that compares is an English made 5” four jaw independent chuck made by Elliott, probably in the 1950’s or 60’s. The little Record Power SC2 I have is also nicely made. The Supernova 2 I have is OK but the
Chuck Jaws are fairly poor quality castings compared to the nicely machined ones of the Axminster shown in the above picture.
Much of the UK can be fairly damp for a good few months of the year so the Stainless Steel construction of the Axminster Chucks and Accessory Jaws shouldn’t be dismissed lightly. Many chucks are plain steel and will rust quite readily under the right conditions. I’ve seen quite a number of rusty chucks and other wood turning equipment offered for sale here in the UK! My Supernova 2 is Nickel plated so has some protection. Accessory jaws however appear to be plain steel. I know the compatible Record Power and Charnwood jaws are.
The registration between the Chuck Jaws and the Accessory Jaws is partly dependent on the tenon. Axminster chucks have a tenon on the Chuck Jaws whilst other makes have the tenon on the Accessory Jaws. I’ve not noticed any difference in alignment between the two types. The fasteners provide the other part of the registration. Once again I’ve not noticed any difference between socket head cap screws and countersunk screws. Countersunk screws shouldn’t in my opinion be relied upon to provide perfect registration.
I’ve found the best way to fit accessory jaws is to follow the manufacturers instructions and not to fully tighten the screws until the jaws have been aligned by closing them.
It’s perhaps worth mentioning that some metal work chucks have two part jaws and I’ve only ever seen them assembled with cap head socket screws. Having said that the design of the jaws appears to provide far better registration between the two parts.
Another feature of the Axminster chucks that is sometimes overlooked is that you can easily remove the Chuck Jaws. This is not possible on some other chucks without taking them apart. This is why I bought an extra set of them which are left attached as seen in my picture. I did strip my Supernova 2 apart and removed the “stop pin” so that I could wind the chuck jaws out if required. But even with it removed the Chuck Jaws still won’t wind out. You can argue about the pro’s and con’s of this but the current Axminster Chuck Jaws have an easily removed “stop screw”. My older Chuck Jaws don’t have this feature.
I think the O’Donnell Jaws are as others have suggested, something of a one trick Pony. As a result I’ve just ordered a set of these to try. Hopefully they’ll prove more useful but then they are half the cost so not so much of an investment.
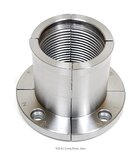