I have an idea for a turned piece which will require holes to be drilled around the stand eventually to have something put into them. Up until now I have managed to to get away with using a spanner on the nut behind the chuck and resting it on the bed, this allowed for either 2, 3or 6 holes to be placed around whatever I was making. I could go about it by buying an indexing plate as my chucks don't have index holes in them, or make one.
A while ago I brought some bits and pieces second hand for the lathe and in the box was the the bracket for a Robert Sorby indexing support which had been modified as can be seen in the photo the bottom bracket had been replaced with a short flat bar. Now mine has two round bars so that is to short, that is not a problem as I have some longer flat bar to replace it with and will make a small block so it sits between the bars as well as making an upright.
The main part however took a little longer to make the index wheel luckily I had some 1/8" thick steel sheet cut this to a little over 6" diameter stuck on a circle with division lines of 24 as I felt that is the most I would ever want.
I drilled a hole in the centre after centre popping to make sure I drill exactly centre(well exactly as much as you can with just a drill press). I used a jig so that the division lines went straight across under a straight edge that sat on two dowels so it did not move and then drilled the outer index holes. Now after all this I wish I took more photo's.
Using the same jig I rotated the disc in front of the grinder this made it nice and round.
I took the opportunity at this sage to use a hole saw to enlarge the centre hole to fit my lathe.
So as of tonight I am at this stage along with the replacement bottom bar cut to length ready for a hole. Also note that so I don't confuse myself when using it I numbered every even numbered hole.
I will post more when I get around to it as well as the jig which will not be until late tomorrow as I have to go for scans tomorrow and I know I will be at the hospital for at least 3 hours what a pain
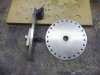
A while ago I brought some bits and pieces second hand for the lathe and in the box was the the bracket for a Robert Sorby indexing support which had been modified as can be seen in the photo the bottom bracket had been replaced with a short flat bar. Now mine has two round bars so that is to short, that is not a problem as I have some longer flat bar to replace it with and will make a small block so it sits between the bars as well as making an upright.
The main part however took a little longer to make the index wheel luckily I had some 1/8" thick steel sheet cut this to a little over 6" diameter stuck on a circle with division lines of 24 as I felt that is the most I would ever want.
I drilled a hole in the centre after centre popping to make sure I drill exactly centre(well exactly as much as you can with just a drill press). I used a jig so that the division lines went straight across under a straight edge that sat on two dowels so it did not move and then drilled the outer index holes. Now after all this I wish I took more photo's.
Using the same jig I rotated the disc in front of the grinder this made it nice and round.
I took the opportunity at this sage to use a hole saw to enlarge the centre hole to fit my lathe.
So as of tonight I am at this stage along with the replacement bottom bar cut to length ready for a hole. Also note that so I don't confuse myself when using it I numbered every even numbered hole.
I will post more when I get around to it as well as the jig which will not be until late tomorrow as I have to go for scans tomorrow and I know I will be at the hospital for at least 3 hours what a pain
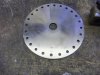
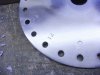
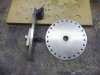
Last edited: