I'm working on an end grain piece of maple that I'm planning on shaping into a heart-ish/baloon form. It's green wood and I'm turning it to finished dimensions (about 3/16ths thick) while wet. It's about 12 inches tall (plus a tenon) and about 10 inches wide near the top. I'll be using a steady rest for the hollowing.
My issue is wanting the get the base as narrow as possible, before I start hollowing. Because I'm going to finish it while wet, it's going to be out of round by the time I get it hollowed out. I think this means that I can't go back, after it's hollowed and make the base above the tenon more narrow, because the piece will likely no longer be perfectly round and I may not have enough thickness in the walls to take it back to round.
I've attached a rough drawing of the HF below. What I'm wondering, is how narrow can I get the area above the tenon (at my red lines) while keeping enough stability in the piece to hollow without getting into significant vibration, or worse, having it snap off above the tenon? The tenon itself is 3.5 inches in diameter. Do you think I could take that base area above the tenon down to a 2 inch diameter...what about 1.5 inches?
Thanks for any help,
Grey
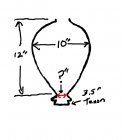
My issue is wanting the get the base as narrow as possible, before I start hollowing. Because I'm going to finish it while wet, it's going to be out of round by the time I get it hollowed out. I think this means that I can't go back, after it's hollowed and make the base above the tenon more narrow, because the piece will likely no longer be perfectly round and I may not have enough thickness in the walls to take it back to round.
I've attached a rough drawing of the HF below. What I'm wondering, is how narrow can I get the area above the tenon (at my red lines) while keeping enough stability in the piece to hollow without getting into significant vibration, or worse, having it snap off above the tenon? The tenon itself is 3.5 inches in diameter. Do you think I could take that base area above the tenon down to a 2 inch diameter...what about 1.5 inches?
Thanks for any help,
Grey
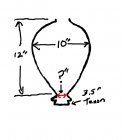