Multi-axis is one of my interests. There are some issues with it though, like blending between the turning axes. So I thought maybe doing it on the CNC could solve that.
First off was to come up with a design. A tallish vessel like a weed pot would be a good start. Design a profile of one side, then modify that for the opposite profile using a graphics program. Then convert it to a surface model for viewing from any angle. IMO, having the multiple profiles adds to the interest (but, what do I know about design?).
The surface model in CAD is sliced at horizontal intervals which become the cutter path. Each horizontal slice has a circular cross section. Off setting the circles from the vertical central axis creates the effect of multi-axis.
The cutting is done with the part standing vertically with a thin wood shaper cutter revolving around the part. The cutter spirals down the part leaving surface that almost doesn't need sanding.
And the completed "turning". For technical reasons the part is not quite as tall and thin as the surface model
How many here are involved with CNC machines? They seem to be slow to catch on with woodturners.
First off was to come up with a design. A tallish vessel like a weed pot would be a good start. Design a profile of one side, then modify that for the opposite profile using a graphics program. Then convert it to a surface model for viewing from any angle. IMO, having the multiple profiles adds to the interest (but, what do I know about design?).
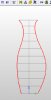
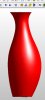
The surface model in CAD is sliced at horizontal intervals which become the cutter path. Each horizontal slice has a circular cross section. Off setting the circles from the vertical central axis creates the effect of multi-axis.
The cutting is done with the part standing vertically with a thin wood shaper cutter revolving around the part. The cutter spirals down the part leaving surface that almost doesn't need sanding.
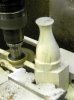
And the completed "turning". For technical reasons the part is not quite as tall and thin as the surface model
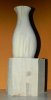
How many here are involved with CNC machines? They seem to be slow to catch on with woodturners.