Hi
I’m making all-in-one salt shaker/ pepper mills. The idea is from this article in American Woodturner.
community.woodturner.org
It relies on a tapered hole in the pepper mill and a matching tapered tenon to hold the salt shaker in place. I’m having trouble getting the tapered hole accurate enough to hold the salt shaker in place and be able to release for filling.
I did get one to work by making a tapered mandrel with sandpaper on it to true up the hole after shaping it with a gouge, but it’s very time consuming and still a bit sloppy.
How would you make a 1 1/2” hole with an accurate taper?
Here’s a picture of the first one
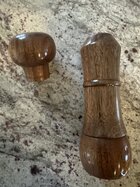
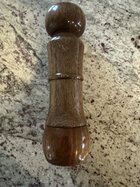
I’m making all-in-one salt shaker/ pepper mills. The idea is from this article in American Woodturner.
Community Portal

It relies on a tapered hole in the pepper mill and a matching tapered tenon to hold the salt shaker in place. I’m having trouble getting the tapered hole accurate enough to hold the salt shaker in place and be able to release for filling.
I did get one to work by making a tapered mandrel with sandpaper on it to true up the hole after shaping it with a gouge, but it’s very time consuming and still a bit sloppy.
How would you make a 1 1/2” hole with an accurate taper?
Here’s a picture of the first one
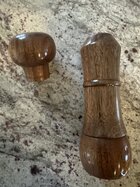
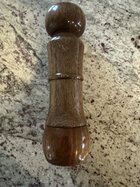