Is this a bad idea? If so, why? And how bad?
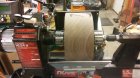
The photo is just a mock up of what I'm considering. The tailstock chuck is not attached in the photo, just pressed against the blank. If I do this for real there will be a chuck on a tenon at the headstock and a second chuck on a tenon at the tailstock. The tailstock will have a Robust live center and chuck adapter. The tail stock could be free to move on the ways, but I'm thinking it should be secured. RPM would probably be between 1200 and 2000.
The goal is to be able to repeatedly reverse the mounting while accurately maintaining alignment. There may be other solutions, but my primary interest is an evaluation of this one. So if it's a bad idea, why and how bad?
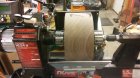
The photo is just a mock up of what I'm considering. The tailstock chuck is not attached in the photo, just pressed against the blank. If I do this for real there will be a chuck on a tenon at the headstock and a second chuck on a tenon at the tailstock. The tailstock will have a Robust live center and chuck adapter. The tail stock could be free to move on the ways, but I'm thinking it should be secured. RPM would probably be between 1200 and 2000.
The goal is to be able to repeatedly reverse the mounting while accurately maintaining alignment. There may be other solutions, but my primary interest is an evaluation of this one. So if it's a bad idea, why and how bad?
Last edited: