If anyone has used either of these, I would love to hear your experience with it. If anyone has the Grizzly setup, Could you give me an idea of how big it goes, and what is the length of the rails that attach to the bandsaw, and how long is the piece the log sled slides on?
I'm getting frustrated with the small size of the table on my bandsaw. I have a 1990's 14" Delta with riser and 2hp motor. I was considering moving up to new saw, but I'm seeing that the tables on anything under ~$3k are not much bigger than what I have. An inch or two at most. in addition, they mostly come with roller guides. After my experience with the Carter roller bearings upgrade, I'd like to stay with rub blocks. The roller bearings were noisy, gummed up a lot, and were quite fiddly to get adjusted properly. The Laguna uses ceramic guides, but I'm afraid to buy Laguna due to the poor customer service. I don't see any rub block guides offered as retrofit for other bandsaws (like the Rikon 18" professional). To top it all off, I'm not sure how I would get a 3 or 400 pound bandsaw down the cellar stairs. Would need to do quite a bit of disassembly. So now I'm considering making a bigger table. The only sticking point is I use the rip fence a LOT, so I would need to find a way to lengthen my rip fence. I could not find any off the shelf kits for a larger table with rip fence, and the aftermarket rip fences don't seem as nice as the one I have.
This has led me to look at the Littel Ripper or Grizzly Log Sled as a solution to my problem. It's really when dealing with chunks of logs that I have the issue with the smaller table, and both of these are designed for just that. The actual log gripper part looks almost identical on these two, and cost is similar but there are some other differences:
* The little ripper offers extensions to work with both larger diameter and length. Up to 8' long and 14" diameter. The Grizzly web site does not say how big it can go in length OR diameter.
* The "Universal Rails" on the Little Ripper would allow me to use my existing rip fence. but without expanding the table. The Grizzly rails look like they are longer, and would allow me to add a couple inches on each side and front of the table using the rails as support, but I would need to use the Grizzly sled as a rip fence. I'd lose the micxro adjustment that I have on my existing fence. I don't do any resawing, so the height is not a problem.
Here is a link to the little Ripper:
stockroomsupply.com
Here is a link to the Grizzzly rails:
www.grizzly.com
and the Grizzly Log gripper:
www.grizzly.com
Obviously, this would be MUCH cheaper than a new bandsaw, and would still be useable if I did upgrade the saw in the future.
Thanks!
I'm getting frustrated with the small size of the table on my bandsaw. I have a 1990's 14" Delta with riser and 2hp motor. I was considering moving up to new saw, but I'm seeing that the tables on anything under ~$3k are not much bigger than what I have. An inch or two at most. in addition, they mostly come with roller guides. After my experience with the Carter roller bearings upgrade, I'd like to stay with rub blocks. The roller bearings were noisy, gummed up a lot, and were quite fiddly to get adjusted properly. The Laguna uses ceramic guides, but I'm afraid to buy Laguna due to the poor customer service. I don't see any rub block guides offered as retrofit for other bandsaws (like the Rikon 18" professional). To top it all off, I'm not sure how I would get a 3 or 400 pound bandsaw down the cellar stairs. Would need to do quite a bit of disassembly. So now I'm considering making a bigger table. The only sticking point is I use the rip fence a LOT, so I would need to find a way to lengthen my rip fence. I could not find any off the shelf kits for a larger table with rip fence, and the aftermarket rip fences don't seem as nice as the one I have.
This has led me to look at the Littel Ripper or Grizzly Log Sled as a solution to my problem. It's really when dealing with chunks of logs that I have the issue with the smaller table, and both of these are designed for just that. The actual log gripper part looks almost identical on these two, and cost is similar but there are some other differences:
* The little ripper offers extensions to work with both larger diameter and length. Up to 8' long and 14" diameter. The Grizzly web site does not say how big it can go in length OR diameter.
* The "Universal Rails" on the Little Ripper would allow me to use my existing rip fence. but without expanding the table. The Grizzly rails look like they are longer, and would allow me to add a couple inches on each side and front of the table using the rails as support, but I would need to use the Grizzly sled as a rip fence. I'd lose the micxro adjustment that I have on my existing fence. I don't do any resawing, so the height is not a problem.
Here is a link to the little Ripper:
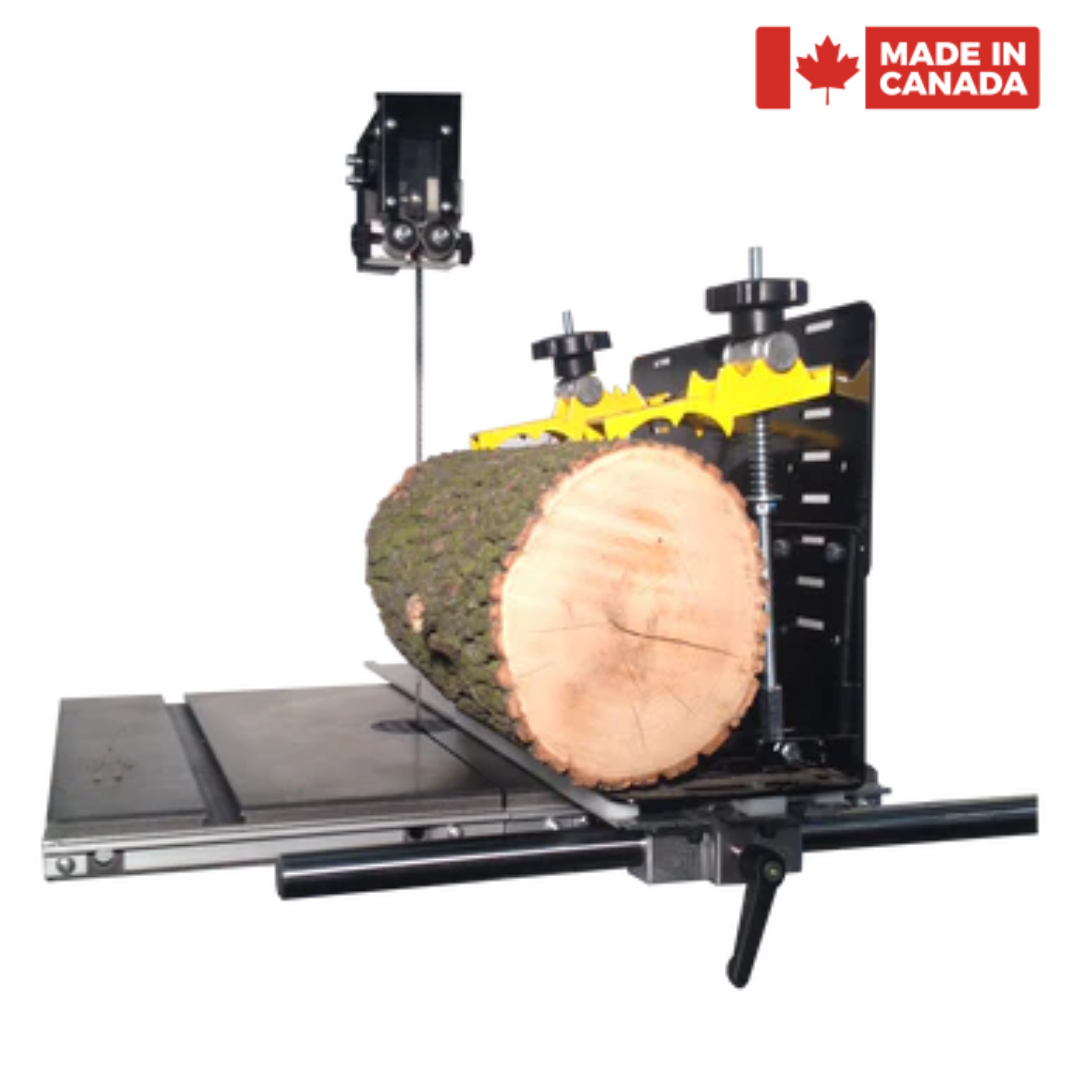
Little Ripper Mini Sawmill and Sliding Track Basic Package - Stockroom Supply Tools
Turn your bandsaw into a mini portable saw mill with The Little Ripper, perfect as a mini log mill and for resawing boards. Safe, precise, and fits any bandsaw. Made in Canada. Purchase online.

Here is a link to the Grizzzly rails:
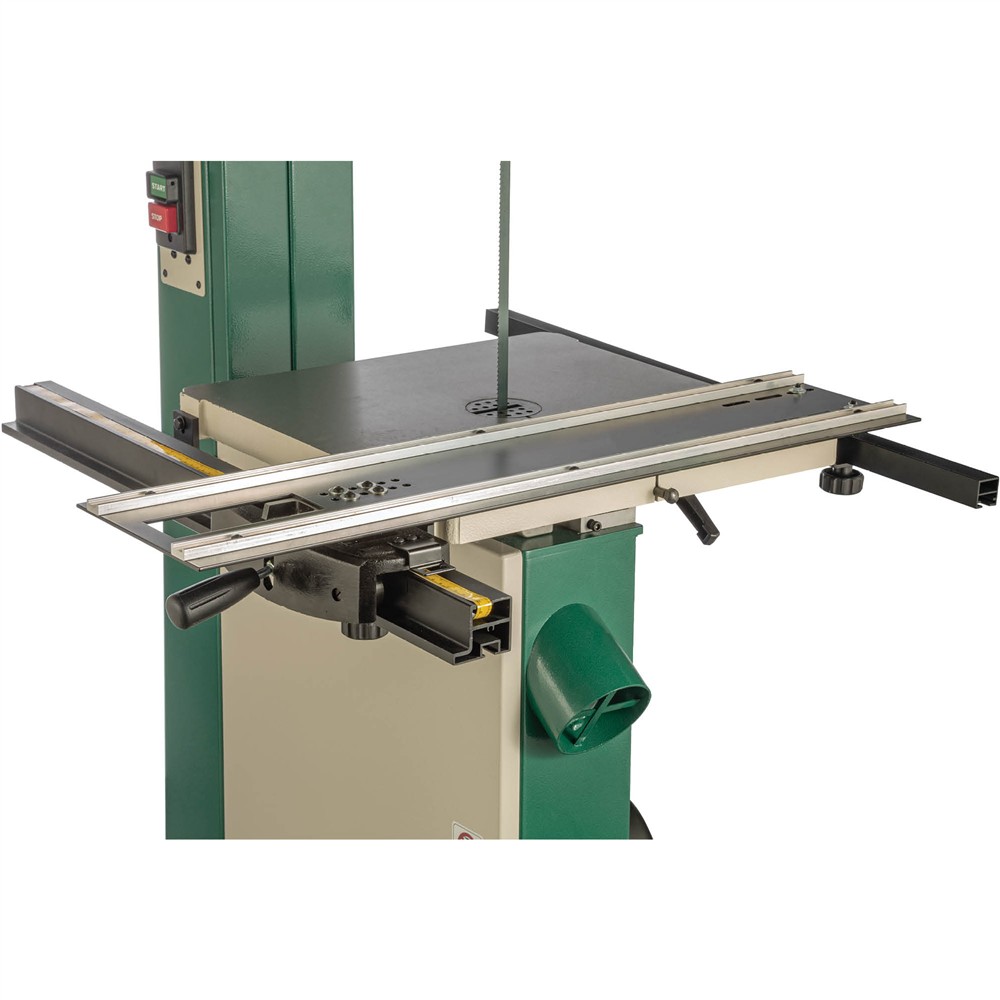
Grizzly T32838 - Bandsaw Sled - Grizzly Industrial, Inc.
<h1>T32838 17" Bandsaw Sled </h1> <h2>Turn your 17" bandsaw into a mini sawmill. </h2> <p>The T32838 Bandsaw Sled fits 17" vertical wood-cutting bandsaws with tables between 12-7/8"–18-1/2" long. <p>The sled includes extruded aluminum front and back rails that allow the bandsaw sled to slide...

and the Grizzly Log gripper:
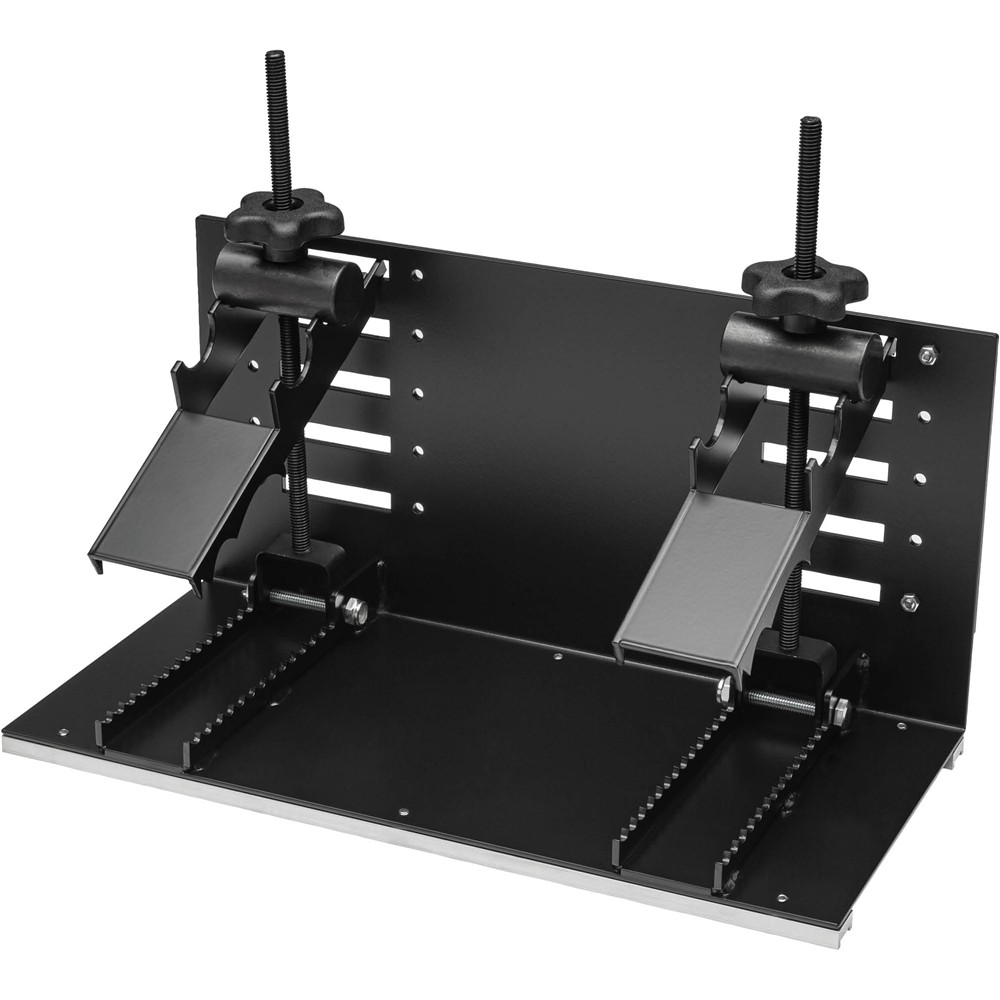
Grizzly T32841 - Sliding Log Milling Jig - Grizzly Industrial, Inc.
<h1>T32841 Sliding Log Milling Jig </h1> <h2>The easy-to-use sliding log milling jig allows you to rip logs lengthwise. </h2> <p>The 32841 Sliding Log Milling Jig rip cuts logs at least 17-3/4" long and up to 11-3/4" in diameter on 17" bandsaws. <p>Secure your workpiece with the adjustable claw...

Obviously, this would be MUCH cheaper than a new bandsaw, and would still be useable if I did upgrade the saw in the future.
Thanks!