I've probably had ten back braces over the years to keep from straining my back with my fixed headstock Woodfast lathe. When I do my undercut rims, it gets especially hard on my back. I've been using this Copperfit X-back brace with its X configuration and stiff staves for about a month now, and it's the best brace I've had to date.
Just passing along what has been a great back support from someone who has had a difficult time with back issues while lathe turning.
=o=
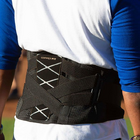
Video at link:
getxback.com
Just passing along what has been a great back support from someone who has had a difficult time with back issues while lathe turning.
=o=
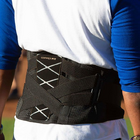
Video at link:
Copper Fit X Back - Superior Back Support & Comfort
ntroducing Copper Fit® X Back Get Optimal Support with Breathable Comfort! Experience Dynamic Support and Unparalleled Stability with our innovative lower back brace. This advanced ergonomic design embodies a next-generation support system, offering full coverage and unmatched comfort, setting...
