- Joined
- Oct 7, 2009
- Messages
- 128
- Likes
- 16
When making clocks up like John Lucas did here in this photo is it better to run the grain horizontal or vertical or does it not matter?? Beinging you are end grain gluing in either case. What would be some of the do's and don'ts using this type segmenting system. ???? I am asuming whatever way you start to keep this grain pattern and do not shift from horizontal to vertical if wanting to add a banding??? Thanks.
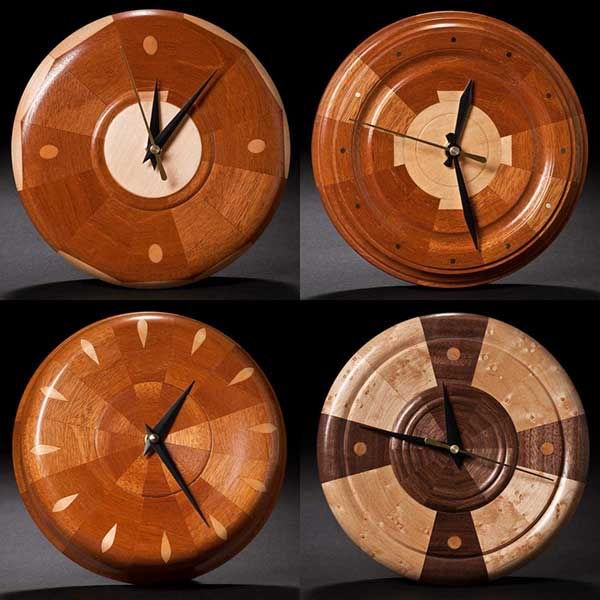