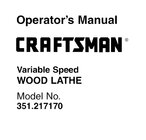
(And thanks, I’m not seeking opinions about whether this is a good lathe. Just helpful comments, please. TIA)
Beat me to it. I used to see that a lot on Kohler starter motors when I was in the OPE business - starter would get hot (due to engine overheating/ lack of maintenance) and all kinds of magnets could come loose from their original epoxy glue - not just starters either, but flywheel magnets (for alternators) were also a common issue (more often on twin opposed engines which were notorious for being tucked in to small engine compartments and never getting the cooling systems maintained) Also even a bit of impact on the housing of the motor can cause magnets to crack or separate, so when seeing that sort of rubbing given the magnets in the housing, one of the first things I'd do is a close inspection of the magnets - Another possibility is the end cap (which also holds the bearing for the rotor shaft) could have shifted or torqued a little bit allowing the rotor to shift slight off center of where it should be (were any of the through bolts even slightly loose?) Just a few things to think on, perhaps but if its out of your depth a motor repair shop (or starter generator shop, etc) may be of some help to resolve it...Are the magnets still Tightly glued inside the motor housing?
That glue can fail due to heat and/or age.
This seems like a likely cause.Are the magnets still Tightly glued inside the motor housing?
That glue can fail due to heat and/or age.
The resistance is not “scraping”, but “pulses”, like magnetic from sector to sector. There were some metal filings stuck to the magnets. Could these be magnetically connecting to and dragging on the rotor? I tried to remove them all, but challenging.Can you feel whether the resistance is smooth or grinding? I wonder if the coils are shorted. It would have the effect of having 2hp of braking force. One test is to try to rotate with the wires disconnected.
If it is mechanical I would check whether each component is aligned, particularly the gearbox.
Also I just noticed that it's a brushed motor, I would make sure the brushes aren't cooked and each segment of the armature is clean and not shorting to the neighboring contact point.
The brushes had been replaced a couple months ago and look good to my eye. I know how hard the gear reduction turned before - stiff but quite do-able. Now I can barely turn it by hand - very different.The carbon brushes are not shown in the picture but they should be checked. If the brushes are worn down such that they only make intermittent contact with the commutator bars then that would explain why the motor does not get up to speed and appears to pulsate rather the scrap. The planetary gear box would probably make it seem like the motor is bound up when trying to turn it manually at the output end.
I know how hard the gear reduction turned before - stiff but quite do-able. Now I can barely turn it by hand - very different.
Does the pulse still occur when the brushes are removed from contact to the stators? If the system turns freely once the coils are not electricity engaged I would inspect the speed control. Another way to inspect this is to compare forward rotations to reverse. They should be slightly different in feel when trying to rotate against the direction bias of the motor. Ie when the motor is set to forward, it should be harder to rotate it backwards.The resistance is not “scraping”, but “pulses”, like magnetic from sector to sector. There were some metal filings stuck to the magnets. Could these be magnetically connecting to and dragging on the rotor? I tried to remove them all, but challenging.
I had to read this one a few times and I now want to ask: are all the insulating inserts and spacers still where they belong? It sounds like the induction from the magnetic fields are activating windings at intervals but not constantly. I would check the end of the armature on the edge of the commutators to make sure they are not shorting together, for example on the bearing race. By design the surface is machinable to remove contamination and corrosion buildup from heat. There needs to be clean and clear lines between the contacts of the commutator where the insulation strips are located.I think these last two comments are on the right track. I was drilling out the center of a very large block of dense, wet plum wood and the motor was clearly working hard, and getting warm. When the output shaft is turned with the chuck nut and a wrench, (power disconnected, brushes removed) the resistance “pulses”, like skipping from one coil section to the next. Without the magnet stator in place, both the inboard and outboard bearings turn freely and I cannot detect any play. I am confident that bearings, brushes and gear reduction are all ok. As for the magnets, they seem to be glued tightly, but I suppose may have shifted with heating. They do seem to be wear marks of the rotor and a bit of metal filings on the magnets, so something is physically rubbing. I guess it’s off to the repair shop. Thanks to everyone here for assistance!
When the windings in a DC motor armature are shorted the commutator bars will show burn marks on the edges that are caused by the arcing that happens when the brush passes between the bars. The photo of the armature does not show any sign that arcing has occurred.On a further note, I would check the windings for shorting. Getting the motor hot enough can liquify the enamel of the magnet wire creating shorts across the winding. Easy enough to check with a DMM
I typically don't work with this large of brush motors, there is a lot of surface that is blurry and shadowed so I can't see arcing burns (I can trust you are right). The com overall is very discolored, so I guess I would still turn down the surface to up the conductive properties and then perhaps also re-brake-in the brushes.When the windings in a DC motor armature are shorted the commutator bars will show burn marks on the edges that are caused by the arcing that happens when the brush passes between the bars. The photo of the armature does not show any sign that arcing has occurred.
Some turners love to play with, repair, fix up, recondition lathes, and some of us just want to turn wood. Find one of the former to re-home your old lathe, and be content you are the latter.Just for closure on those that gave help. I took the motor and controller to motor repair shop. Without disassembly they tested the motor and say it shorts out. Guessed it needed re-winding at an out-of-state facility, couple hundred bucks estimate. Also said the controller board was defective, putting out AC instead of DC current. No estimate possible as to whether it could be repaired or replaced... All this for a lathe I purchased for just $200, so seemed like a poor investment. I ended up looking at, and eventually buying, a new Laguna 1216. I'm very happy with it (except for the cost, of course....). I figure it should have good resale value. Now I have a vintage monster lathe available to anyone who could benefit / rebuild / part out, etc.
Yeah, too bad it weighs about 200 lbs or the potential market would be larger....Some turners love to play with, repair, fix up, recondition lathes, and some of us just want to turn wood. Find one of the former to re-home your old lathe, and be content you are the latter.